Revolutionizing Construction: The Rise of Prefab office and Structures in 2024
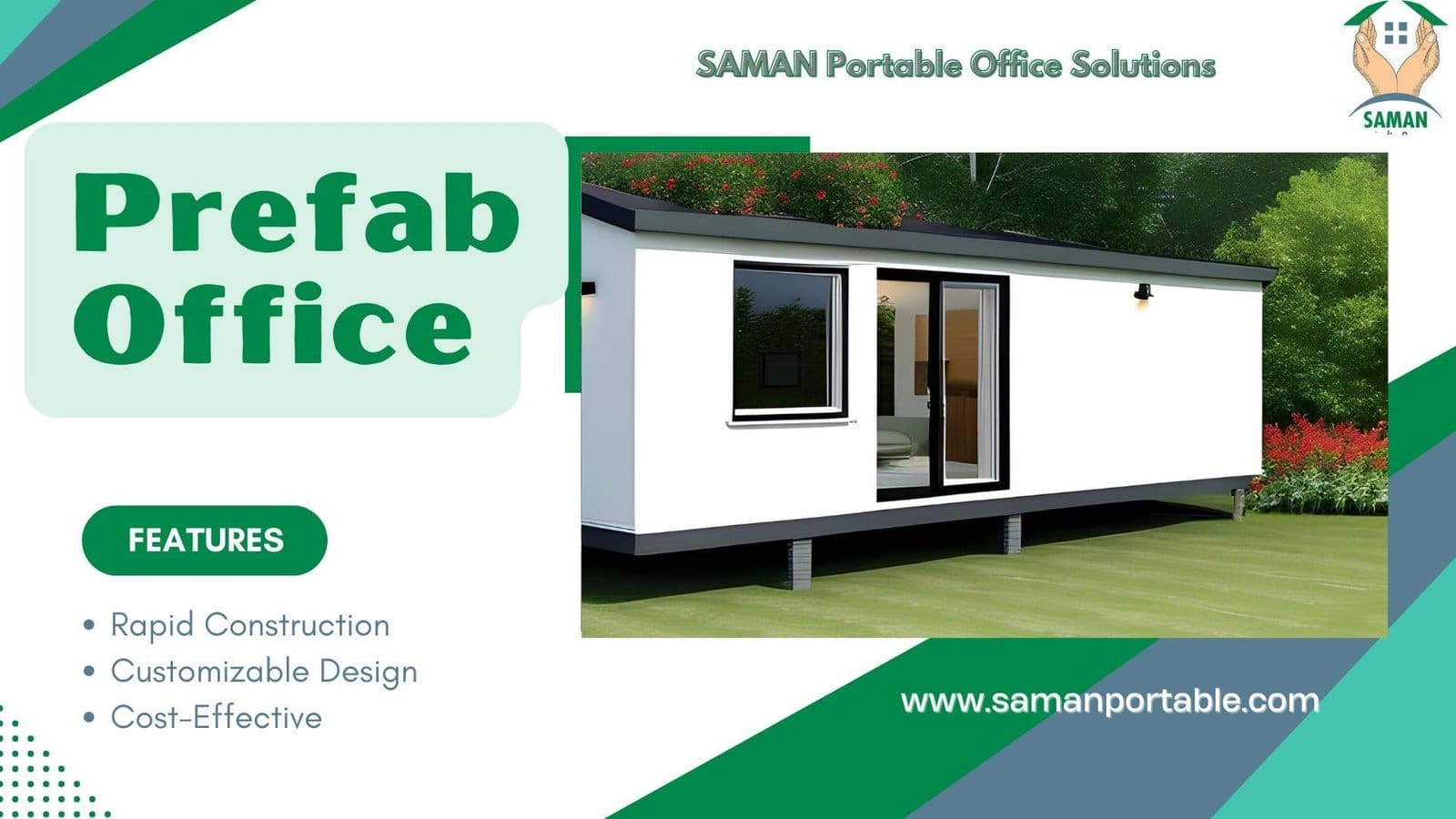
Introduction to Prefab office & Structures
The potential for unprecedented design freedom and faster production rates. Moreover, 3D printing minimizes material waste, reduces transportation costs, and allows for on-demand production of components, further enhancing the efficiency of prefab construction.
Sustainable and Green Aspects of Prefab Office
Energy Efficiency in Prefab Buildings
Prefab Office can be designed to maximize energy efficiency. The controlled factory environment allows for the integration of energy-efficient systems, such as insulation, air sealing, and high-performance windows. Additionally, modular design and improved construction techniques minimize thermal bridging, ensuring superior insulation properties. These energy-saving features contribute to reduced operation costs and a smaller environmental footprint for prefab buildings.
Reduced Construction Waste and Environmental Impact
Prefabrication significantly reduces construction waste as components are precisely fabricated off-site, leading to more efficient material usage. The factory setting allows for better waste management and recycling practices, optimizing resource utilization. Additionally, the controlled manufacturing environment minimizes pollution associated with on-site construction, resulting in a reduced environmental impact overall.
Integration of Renewable Energy Systems
Prefabricated office can integrate renewable energy systems, such as solar panels and wind turbines, to harness clean and sustainable energy sources. The roof and facade of prefab structures can be designed to accommodate solar panels, maximizing energy generation. Combined with energy-efficient features, this integration of renewable energy systems contributes to the sustainability and long-term cost savings of prefab buildings.
Applications of Prefabricated Structures
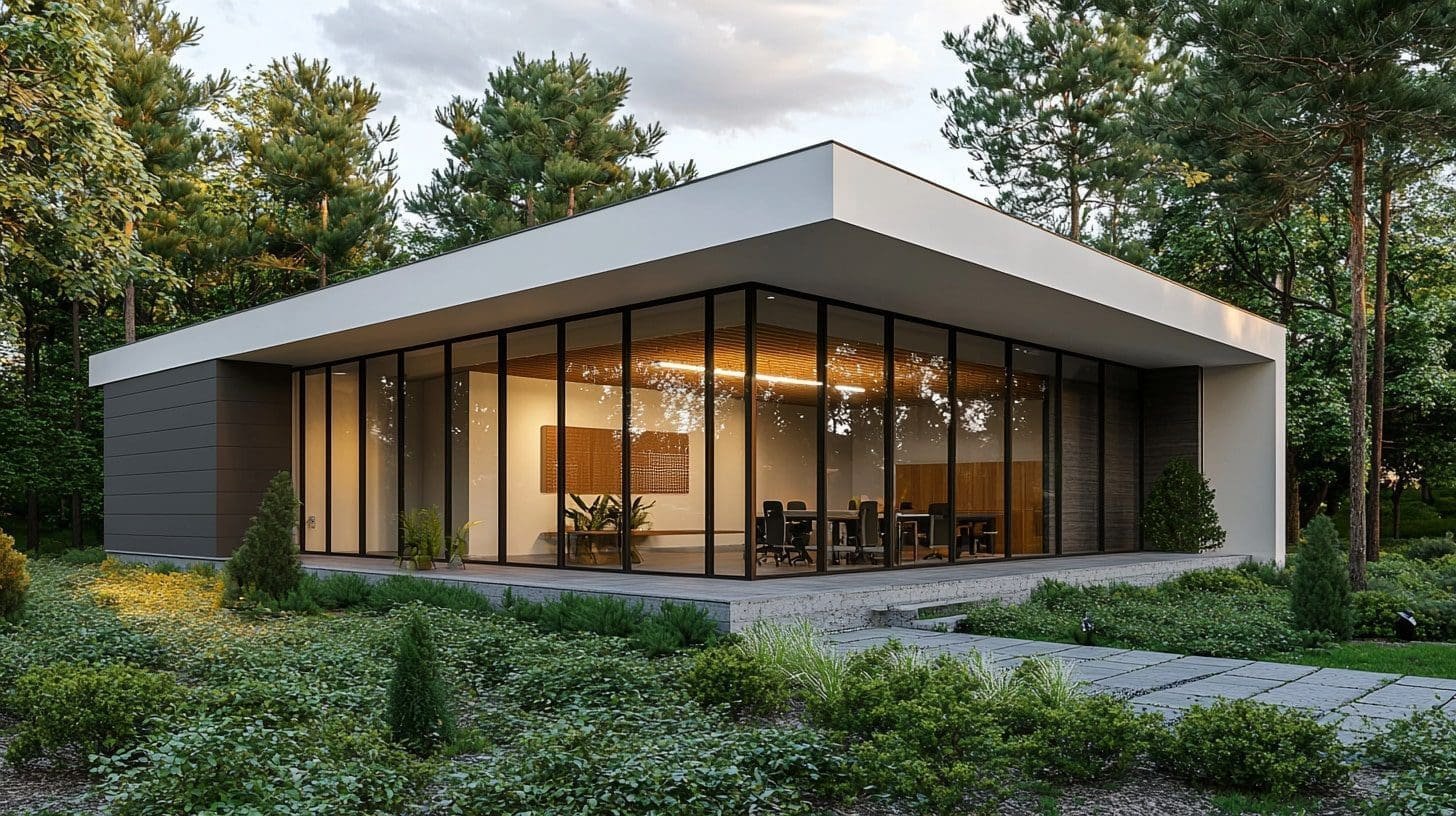
Prefab Homes in Kerala
Residential Prefabs
Residential prefabs offer a modern and efficient alternative to traditional construction methods. They can range from single-family homes to multi-story apartment complexes. Prefabricated residential structures are customizable and can be designed to meet various architectural styles and homeowner preferences. The time-saving nature of prefab construction makes it an attractive option for those looking to expedite the building process while maintaining high-quality standards.
Prefab Office for commercial
Prefabricated offices are well-suited for commercial and office spaces. Companies seeking to expand their facilities quickly can opt for prefab construction to meet their specific spatial needs. Prefab offices and commercial buildings can be easily scaled up or down, allowing for flexibility in accommodating changing business requirements. Furthermore, the controlled manufacturing process ensures that the final product is of excellent quality and aesthetically pleasing.
Prefab Office for Educational and Institutional Use
Prefabricated structures have also found their way into educational and institutional settings. Prefab classrooms, school buildings, and healthcare facilities offer a faster and more cost-effective solution to address the growing demand for educational spaces and medical facilities. These structures can be fully equipped with the necessary amenities, such as classrooms, laboratories, and healthcare equipment, to ensure a conducive learning and healing environment.
Prefab Office for Healthcare and Medical Facilities
The healthcare industry recognizes the benefits of prefabricated construction, particularly in the context of medical facilities. Prefab hospitals, clinics, and specialized healthcare buildings can be customized to meet the unique requirements of the healthcare sector. The controlled construction environment and efficient production processes contribute to reduced project schedules, enabling faster access to essential medical services for communities.
Prefab Office for Disaster Relief
Prefabricated structures play a vital role in disaster relief efforts. They provide quick and efficient shelter solutions for those affected by natural disasters, including earthquakes, hurricanes, and floods. Prefab relief structures can be rapidly deployed and assembled on-site, ensuring the timely provision of temporary housing, medical centers, and emergency response facilities to support affected communities.
Cost Analysis: Prefab vs. Traditional Construction

Container Offices and Porta Cabins by Saman Portable
Initial Costs and Time Savings
Prefab construction often offers significant cost savings compared to traditional construction methods. The streamlined manufacturing process reduces labor costs, as fewer workers are required on-site. The shorter construction timeline translates to reduced financing costs and earlier occupancy, allowing for faster returns on investment. Additionally, prefabrication minimizes the risk of cost overruns associated with weather delays and other unpredictable on-site factors.
Long-term Maintenance and Operational Savings
Prefabricated buildings are designed for durability and require less maintenance compared to traditional structures. The quality control implemented in factory settings ensures that components are built to last, minimizing the need for frequent repairs or replacements. Additionally, the energy-efficient features of prefab structures contribute to long-term operational savings, as reduced energy consumption leads to lower utility bills.
Return on Investment (ROI)
Prefabricated buildings can offer a favorable return on investment due to the cost and time savings inherent in the construction process. The accelerated construction timeline allows for earlier occupancy and revenue generation for commercial and residential projects. The reduced maintenance and operational costs over the lifespan of the building further enhance the overall return on investment.
Challenges and Limitations of Prefabricated Construction
Transportation and Logistics Challenges
Transporting prefabricated components to the construction site can present logistical challenges, especially for larger and more complex structures. Proper planning and coordination are essential to ensure efficient delivery and minimize transportation costs. Additionally, transportation considerations may limit the size and height of the prefab modules or panels. Road restrictions and access to the construction site must also be carefully managed to avoid delays and additional expenses.
Design Limitations and Customization
While prefabricated construction offers versatility, there are limitations when it comes to design customization. Compared to traditional construction, there may be constraints on architectural styles and complex structural designs. However, advancements in prefabrication technology are expanding design possibilities, and architects and engineers are finding innovative ways to push the boundaries of prefab construction.
Building Code and Regulatory Considerations
Prefabricated structures need to comply with local building codes and regulations, just like traditional buildings. There may be specific requirements and certifications that prefab buildings must meet, such as fire safety standards, structural stability, and energy efficiency ratings. Prefab construction companies must ensure that their designs and manufacturing processes align with the relevant building codes and obtain the necessary permits for construction.
Successful Examples of Prefab Office and Structure Projects
Case Studies of Iconic Prefab Buildings
Numerous iconic buildings around the world showcase the potential of prefabricated construction. One notable example is the B2 residential tower in Brooklyn, New York. Standing at an impressive 32 stories, this building holds the distinction of being the world’s tallest modular tower. The efficient construction process allowed for substantial time and cost savings while delivering high-quality housing for residents.
Another prominent prefab building is the Ark Encounter in Kentucky, USA. This massive wooden structure, spanning over 100,000 square feet, was constructed using timber panels manufactured off-site. It serves as a popular tourist attraction and exemplifies the versatility and aesthetic appeal of prefabricated structures.
Innovative Prefab Office Companies
Several innovative companies specialize in prefab construction and have been at the forefront of this revolutionary industry. One such company is Katerra, which combines technology, off-site manufacturing, and design to offer complete building solutions. Katerra leverages advanced automation and robotics to deliver high-quality prefab projects while significantly reducing construction timelines and costs.
New Frontier Tiny Homes is another example of an innovative prefab construction company. They focus on designing and building small, sustainable homes using off-site manufacturing methods. These compact yet well-designed structures meet the demand for minimalistic living while maintaining a high level of craftsmanship.
Future Trends and the Outlook for Prefabricated Structures

Container Office, Porta Cabins and Container Homes by SAMAN Portable
Integration of Smart Technologies
The future of prefab construction lies in the integration of smart technologies. From Internet of Things (IoT) connectivity to energy management systems, smart technologies will optimize the performance, comfort, and sustainability of prefab buildings. This integration will enable real-time monitoring and control of energy usage, indoor climate, and security systems, creating intelligent and responsive living and working environments.
Growing Popularity in Urban Areas
Prefab construction is poised to gain further popularity in urban areas as cities face rapid population growth and the demand for affordable housing surges. The ability of prefabricated structures to be quickly assembled and customized to fit varying site conditions makes them an excellent solution for addressing urban housing shortages. Additionally, prefabs offer an opportunity to revitalize underutilized urban spaces, such as vacant lots or brownfield sites.
Potential Impact on Traditional Construction Industry
The rise of prefabricated structures is likely to disrupt the traditional construction industry. The speed, efficiency, and cost-effectiveness of prefab methods will encourage more developers, architects, and contractors to embrace this construction approach. With advances in technology and increased acceptance of prefab buildings, the traditional construction industry will need to adapt to remain competitive and meet evolving market demands.
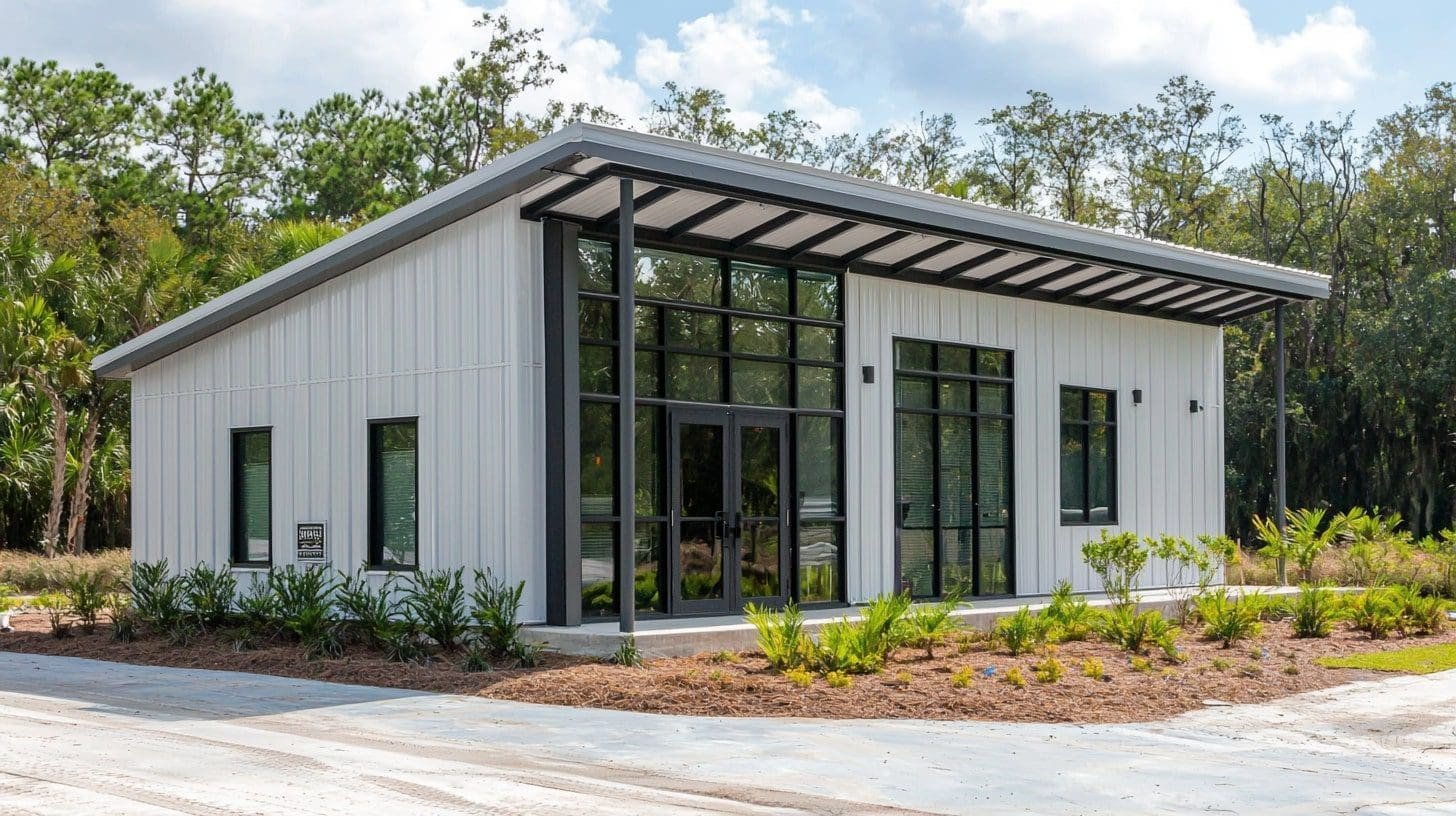
PEB Building Design and Structure
Summary
In summary, prefabricated structures have revolutionized the construction industry by offering faster, more cost-effective, and sustainable building solutions. Prefab buildings are constructed off-site using a variety of materials and construction methods, including modular buildings, panelized construction, steel and concrete prefabs, and pre-engineered metal buildings.
Advancements in prefabrication include digital design and Building Information Modeling (BIM), automation and robotics, and 3D printing. These innovations enhance the efficiency, accuracy, and customization capabilities of prefabricated structures.
Prefab buildings have found applications in residential, commercial, educational, healthcare, and disaster relief sectors. They provide time-saving solutions offers technology This. components for prefabricated structures
Definition and Concept of Prefabrication
Prefabricated structures, also known as prefab buildings or modular construction, are buildings that are manufactured off-site in a controlled factory environment and then transported to the final construction site for assembly. This innovative construction method involves the production of standardized components and modules that can be easily transported and assembled, reducing construction time and labor requirements.
Evolution of Prefabricated Construction
This industry has a long history, dating back to ancient times when civilizations used pre-cut stone blocks for building structures. However, the modern concept of prefab construction began to emerge in the early 20th century with the development of assembly line processes and mass production techniques. Over the years, advances in technology and construction methods have revolutionized the industry, making prefab structures more efficient, durable, and aesthetically appealing.
Advantages of Prefab Office
Prefabricated structures offer numerous advantages over traditional construction methods. One of the primary benefits is the significant reduction in construction time. Since prefab components are manufactured simultaneously with site preparation, the overall construction timeline is considerably shorter. This accelerated process also leads to substantial cost savings due to reduced labor and financing expenses.
Moreover, prefabricated buildings are known for their exceptional quality control. Being produced in a factory environment allows for rigorous inspections at every stage of production, ensuring the highest standards of craftsmanship and precision. Additionally, the controlled setting of the factory minimizes the impact of adverse weather conditions, which can cause delays in traditional construction.
Prefab buildings also contribute to sustainability efforts. The factory production of components results in reduced construction waste and environmental impact. Furthermore, the controlled manufacturing process allows for the integration of energy-efficient systems, creating environmentally-friendly structures that help conserve energy and reduce operational costs in the long run.
Components and Techniques Used in Prefabricated Construction
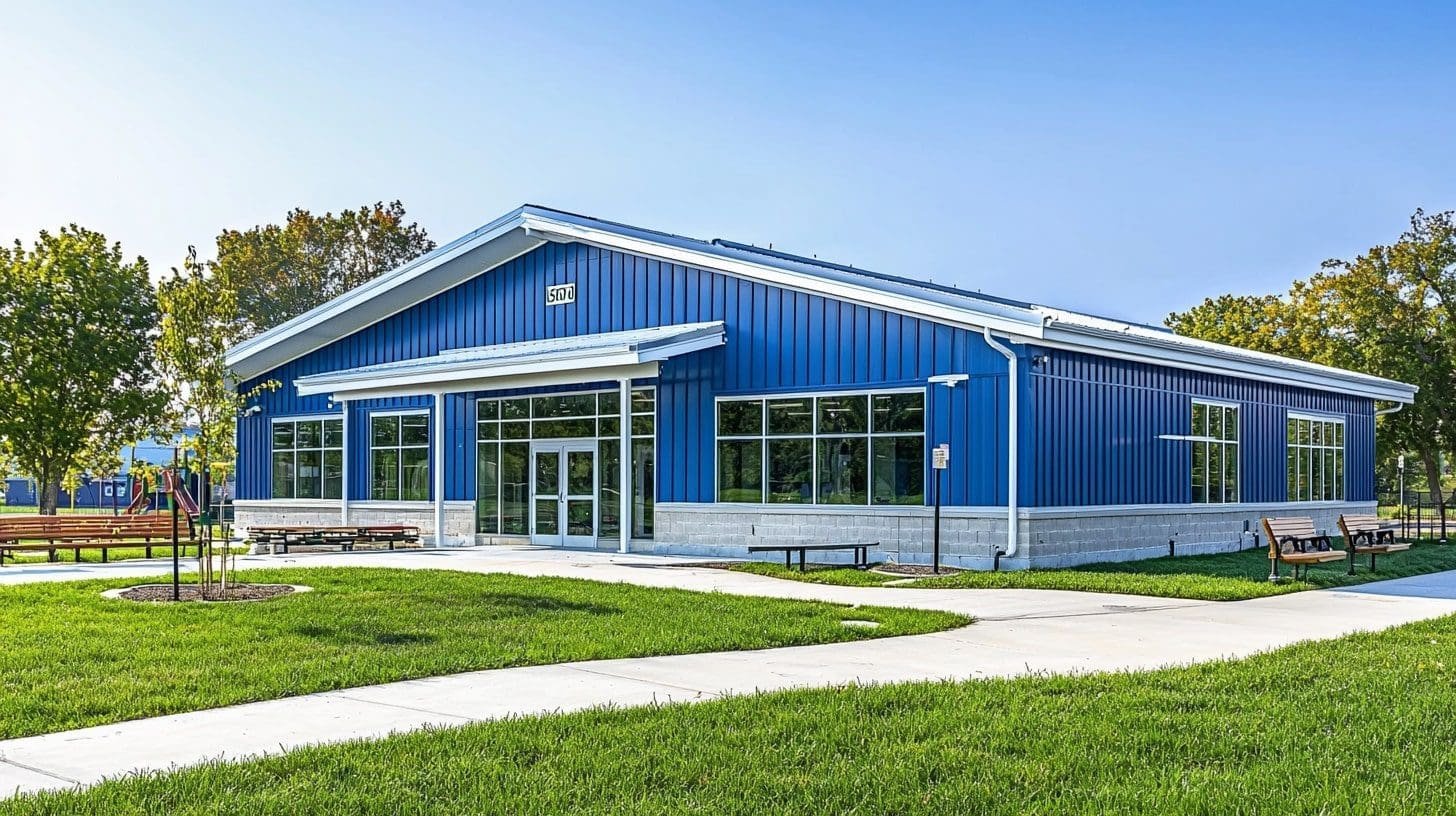
Prefabricated house in Pune
Primary Materials Used in Prefabrication
Prefabricated structures can be constructed using a variety of materials, depending on the desired outcome and the specific building requirements. Some commonly used primary materials include:
- Structural Steel: Steel is a versatile material that offers excellent strength and durability, making it suitable for a wide range of applications in prefab construction.
- Reinforced Concrete: Concrete is known for its high compressive strength and ability to withstand different weather conditions, making it an ideal choice for prefabricated structures.
- Timber: Timber is a renewable resource that can be used for both structural and aesthetic purposes in prefab buildings. It offers a natural, warm aesthetic and provides excellent insulation properties.
- Composite Materials: Composite materials, such as fiber-reinforced polymers (FRPs), offer lightweight and high-strength characteristics, enabling designers and engineers to create innovative and efficient prefab structures.
Off-Site Construction Methods
Off-site construction methods are integral to prefabrication. They involve the manufacturing and assembly of building components in a controlled factory environment, away from the final construction site. Some common off-site construction methods include:
- Panelization: Panelized construction involves the fabrication of wall panels, floor panels, and roof panels in the factory, which are then transported and assembled on-site. This method allows for efficient production and assembly, reducing on-site labor requirements and construction time.
- Volumetric Modular Construction: Volumetric modular construction refers to the manufacturing of complete room-sized modules in the factory, including walls, floors, ceilings, and even plumbing and electrical systems. These modules are then transported to the site and stacked or assembled to form the final structure.
- Hybrid Methods: Hybrid methods combine both on-site and off-site construction techniques. This approach allows for the utilization of traditional on-site construction methods where necessary, while still harnessing the benefits of prefab components and assemblies.
Installation and Assembly Techniques
The installation and assembly of prefabricated structures involve careful planning and coordination. Once manufactured off-site, the components are delivered to the final construction site for assembly. The installation and assembly techniques vary depending on the type of prefab construction being used.
For modular buildings, cranes are often utilized to lift and position the modules onto the foundation or supporting structure. These modules are then interconnected and sealed to ensure structural integrity and weather resistance.
In panelized construction, the pre-fabricated panels are erected, aligned, and fastened together on-site. This assembly process may involve the use of crane equipment and specialized hardware designed for easy installation. Once the panels are secured, additional finishing elements such as cladding, insulation, and windows are added to complete the structure.
Steel and concrete prefabs often involve the use of welded connections and bolts for assembly. These techniques ensure the structural stability and integrity of the building. Pre-engineered metal buildings, which are characterized by pre-designed and pre-fabricated components, are typically assembled using nuts, bolts, and interlocking systems.
Types of Prefabricated Structures
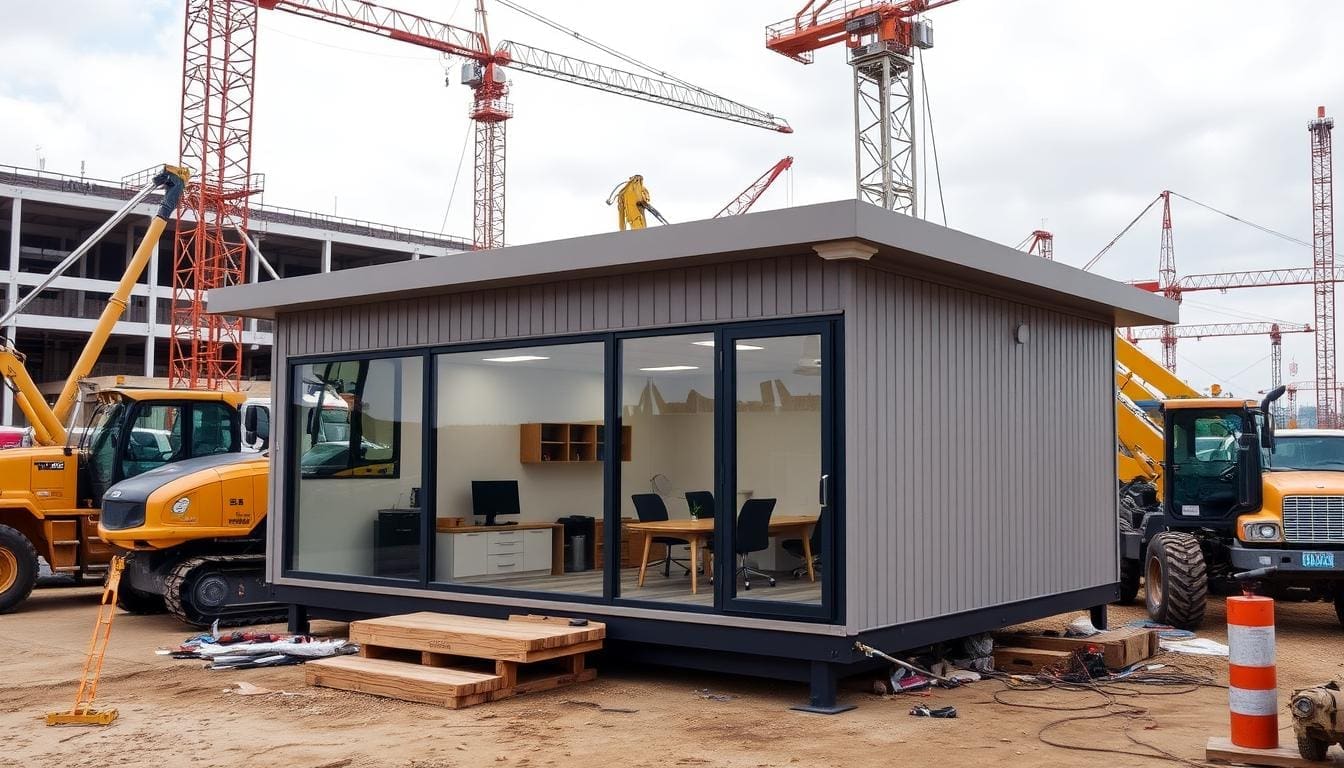
prefabricated site office manufacturers
Modular Buildings
Modular buildings are one of the most well-known types of prefabricated structures. They are constructed using pre-fabricated modules that are manufactured in a controlled factory environment. These modules are fully finished, including interior finishes, electrical wiring, and plumbing. The modules are then transported to the construction site and assembled to form a complete building. Modular buildings offer flexibility, as they can be easily expanded or relocated to meet changing needs.
Panelized Construction
Panelized construction involves the fabrication of wall panels, floor panels, and roof panels in a factory environment, which are then transported to the construction site for assembly. The panels are typically pre-insulated and pre-finished, reducing on-site labor requirements. This method allows for efficient production and assembly, making it suitable for both residential and commercial projects.
Steel and Concrete Prefabs
Steel and concrete prefabs utilize these respective materials as the primary structural elements. Steel prefabs are known for their strength, durability, and flexibility in design. Steel components can be easily fabricated and assembled, making it a popular choice for various types of prefabricated structures, including residential homes, warehouses, and office buildings.
Concrete prefabs, on the other hand, leverage the strength and durability of reinforced concrete to create robust and long-lasting structures. Concrete prefabs offer excellent fire resistance, as well as the ability to withstand extreme weather conditions. They are often used for industrial buildings, parking structures, and high-rise residential projects.
Pre-engineered Metal Buildings
Pre-engineered metal buildings (PEMBs) are complete building systems that are manufactured and designed by specialized firms. These buildings consist of pre-designed and pre-engineered components, including steel frames, roof systems, and wall panels. PEMBs are highly versatile and commonly used for warehouses, factories, and agricultural structures.
Advancements and Innovations in Prefabrication
Digital Design and Building Information Modeling (BIM)
Digital design and Building Information Modeling (BIM) have revolutionized the prefabrication industry. BIM provides a virtual representation of the building, allowing architects, engineers, and contractors to collaborate seamlessly throughout the design and construction phases. This technology enables more accurate design planning, clash detection, and optimization of the modular components, leading to improved efficiency and reduced errors in prefab construction.
Automation and Robotics in Prefab Construction
Automation and robotics have been increasingly incorporated into prefab construction processes. Robotics can perform repetitive tasks with precision and efficiency, reducing the need for manual labor. Assembly lines equipped with robots can manufacture components, such as wall panels or modules, at a faster rate, improving production time and consistency. Automation also allows for better quality control, as machines can ensure precise measurements and alignments during assembly.
3D Printing in Prefabrication
3D printing, or additive manufacturing, has gained traction as an innovative method in prefab construction. By layering materials to create three-dimensional objects, 3D printers can produce intricate and customizable