Exploring the Benefits and Applications of Modern Prefab Labour Colonies: A Comprehensive Guide
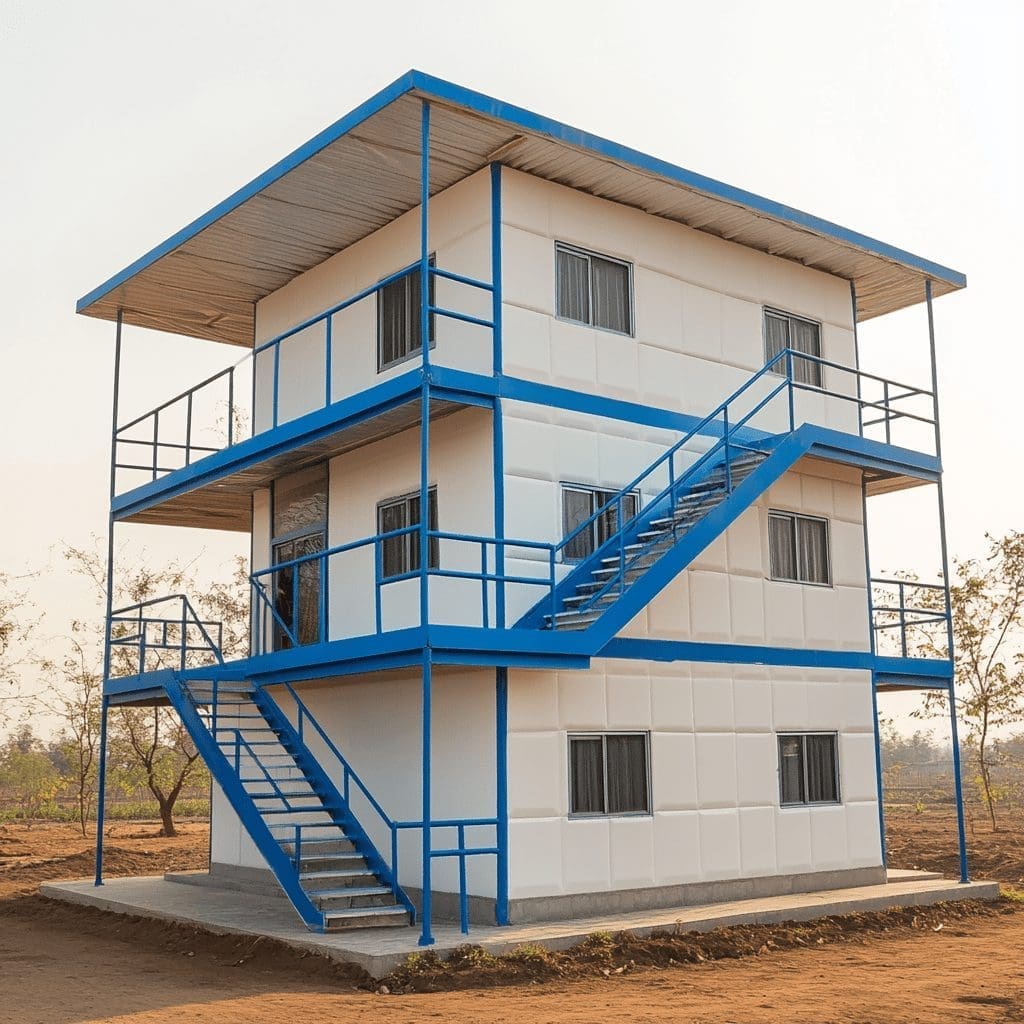
In India’s fast-paced construction scene, a new way to house workers is emerging. Modern prefab labour colonies are leading the charge. They offer something unique and could change how we view temporary housing for workers. Let’s explore the world of prefabricated labour colonies and the exploring prefab cottages to see what makes them special.
Imagine buildings arriving almost ready, with workers moving in just days or weeks. This is a key benefit of prefab labour colonies. They are built mostly in controlled settings, ensuring top quality, safety, and speed. This new approach is raising the bar for workforce housing.

Key Takeaways:
- Prefabricated buildings can be delivered up to 90% complete, allowing for rapid occupancy.
- 90% of the construction process occurs in controlled environments, ensuring quality and safety.
- Prefabricated construction can complete projects in about half the time compared to traditional methods.
- Modular portable cabins have a lifespan of over 30 years and can exceed their original purposes.
- Prefabricated construction is environmentally friendly, reducing waste and resource consumption with sustainable prefab solutions.
Understanding Prefabricated Construction: Historical Evolution and Basics
Prefabricated construction has a long history. It started with nomadic people needing easy-to-move shelters. The idea grew a lot during colonization and really took off in the 20th century, especially during and after World Wars.
Origins and Development Through Time
The need for quick housing led to prefabricated structures. As people moved more, the need for temporary homes grew. Over time, new materials and better ways to make these homes improved a lot.
Key Components of Prefab Construction
- Walls: Made off-site, they provide strength and keep the inside warm or cool.
- Roofs: Designed to fit many styles, they meet different needs.
- Floors: Made to be easy to put in and keep the same quality everywhere.
Modern Manufacturing Processes
Today’s prefab construction uses new, efficient ways to make things. This includes advanced welding, making concrete parts ahead of time, and using BIM for better planning. Prefab workforce housing must follow the same rules as regular houses, like the International Building Code in the U.S.

Labor Sheds for Sale
Modern prefab construction offers many advantages. It’s cheaper, better quality, faster, and better for the environment. As more people need portable homes, prefab is changing how we build.
The Rising Demand for Modern Prefab Labour Colonies in India
The need for modern modular worker colonies, affordable prefab labour housing, sustainable prefab labor colonies, and energy-efficient labor housing in India is growing fast. This is because of the country’s quick urban growth and the need for new infrastructure ideas.
India’s urban population is expanding quickly. This means more people need homes that are both affordable and quick to build. Prefab construction is a good answer, offering affordable prefab labour housing that’s faster to put up than regular houses. In fact, prefab colonies can be built 90% off-site, cutting down on time and money.
- Over 100 prefab products are available on IndiaMART under the category of Prefabricated Houses & Structures.
- Prefabricated Bali Huts are priced at ₹320 per sq ft and are commonly used for applications such as farmhouses, luxury farm villas, bamboo resorts, and cottages.
- Prefabricated Staff Huts are priced at ₹600 per sq ft and are typically used for office and construction site applications.
The push for sustainable prefab labor colonies is also growing. There’s a bigger focus on using green materials and designs that save energy. This meets the demand for energy-efficient labor housing that’s good for the planet and comfy for workers.
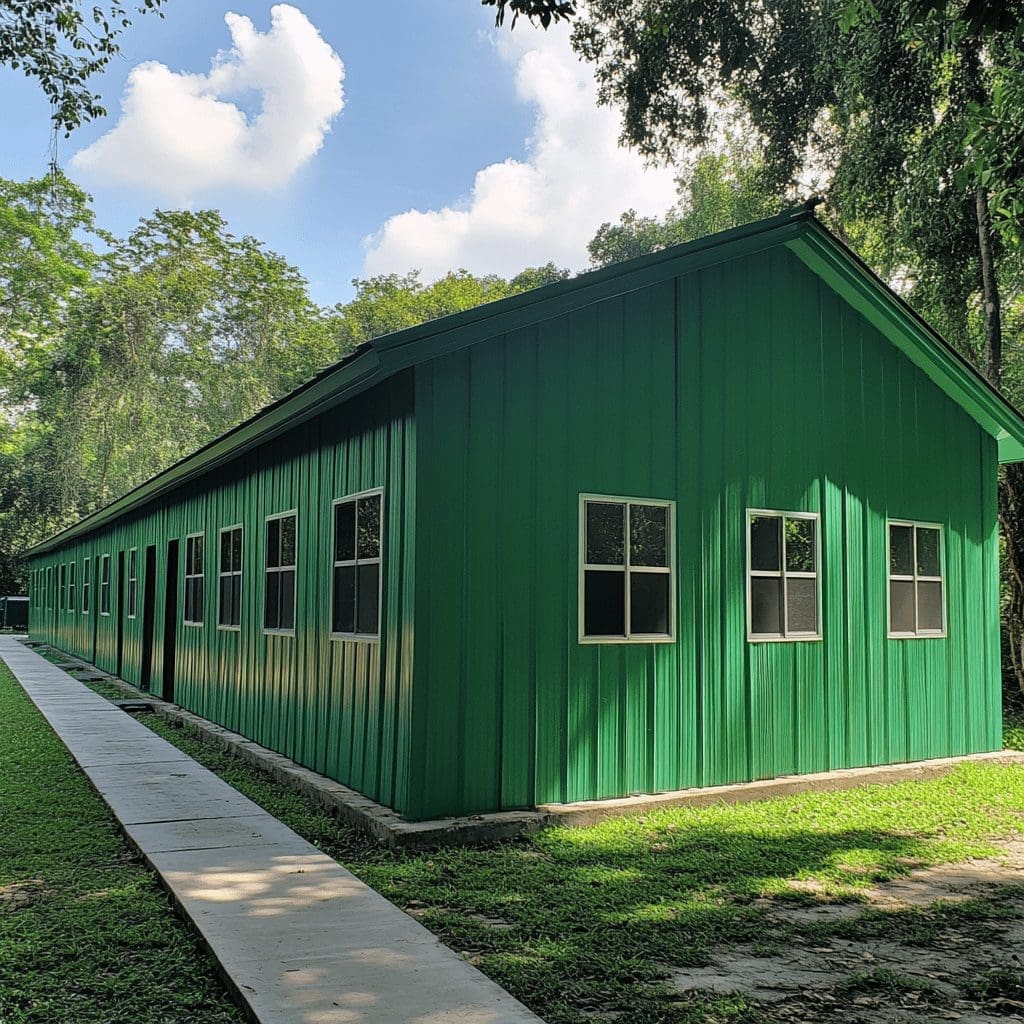
Labor Sheds for Sale in Bangalore
Also, modern modular worker colonies are popular because they’re flexible and can be customized. Developers and groups can adjust the design and features of customizable prefab housing to fit their needs. This ensures the affordable prefab labour housing solutions really meet the special needs of their projects.
Essential Features and Design Considerations
SAMAN Portable focuses on key features for modern workforce prefab housing. Their portable prefab worker housing stands out. It lasts over 15 years, thanks to top-quality, rust-proof, and weather-resistant materials.
Their customizable prefab labor housing is durable and easy to move. This makes it perfect for different project needs.
Space Optimization and Layout Planning
Using space wisely is key in prefab labor colonies. SAMAN Portable uses advanced steel framing. This ensures a well-planned layout that saves space.
This focus on detail means workers live comfortably. They don’t lose out on functionality or easy access.
Material Selection and Durability
Durability is crucial in modern workforce prefab housing. SAMAN Portable Office Solutions picks the best steel and insulation. This makes their portable prefab worker housing strong and long-lasting.
These eco-friendly labor colonies need little upkeep. They offer a reliable housing solution for workers.
Safety and Compliance Standards
Following safety and compliance rules is essential in customizable prefab labor housing. SAMAN Portable Office Solutions checks their structures carefully. They make sure they meet all safety standards.
This dedication to safety ensures a secure living space for workers. It also meets all necessary regulations.
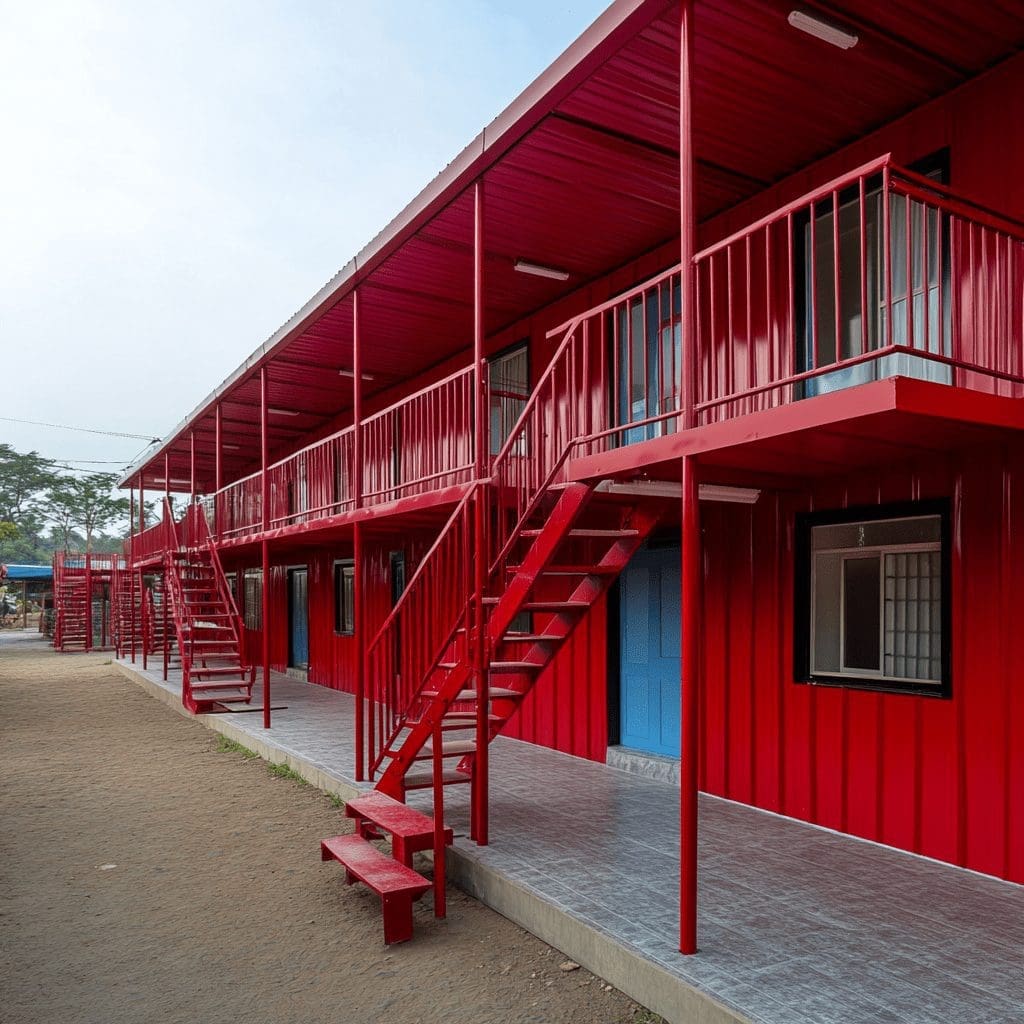
Labor Shelters
Cost Analysis and Economic Benefits
Cost-effective prefab housing brings big economic wins, mainly through better efficiency and saving time. The first cost might be a bit more than traditional methods. But, prefab’s benefits really shine when you start building.
Prefab buildings can be finished in half the time of regular construction. This means big savings on labor and on-site costs. Plus, prefab’s controlled making process cuts down on waste, making it more cost-effective.
- Studies show prefab can save 21% on costs, 47% on time, and boost productivity by 10%.
- The benefits of prefab depend on the building type, location, and how it’s made. Scale, standardization, and environmental impact also play a role.
- Prefab is seen as a green way to build. It can make construction better, quality higher, and more productive.
Also, prefab’s ability to be reused or moved is a big plus for businesses. It’s great for companies that need to change their worker housing often. This lets them adjust their housing to fit their needs, saving money in the long run.
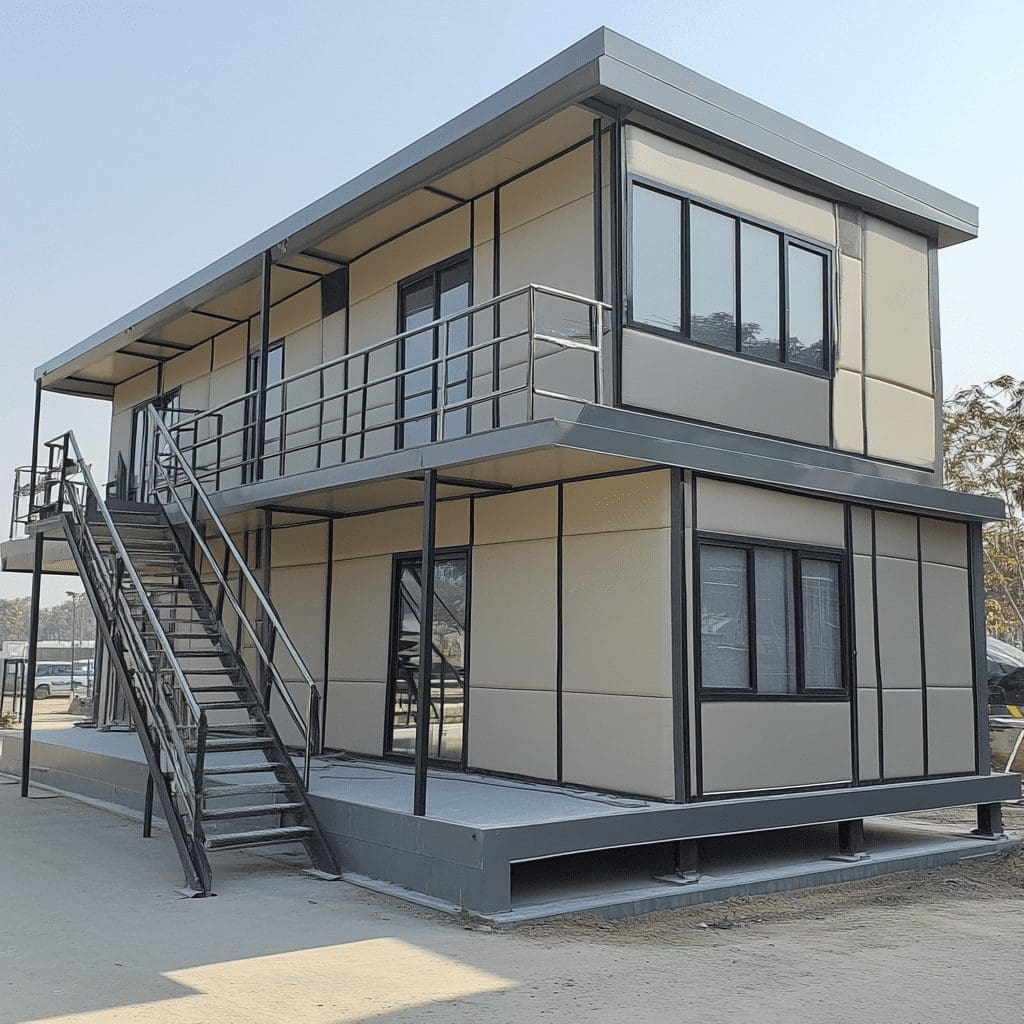
Labor Shelters ready For Installation
In summary, prefab construction is cost-effective and fast. It’s a smart choice for businesses looking to save money on labor and site setup.
Environmental Impact and Sustainability Aspects
Prefabricated construction is better for the environment than building on-site. It uses prefab labor camp, modular worker housing, and prefabricated workforce housing to cut down environmental harm. This way, construction projects can be more eco-friendly and sustainable.
Energy Efficiency Measures
Energy efficiency is a big deal in prefab construction. Designs aim to save energy and cut down on costs. They use energy-saving appliances, better insulation, and solar panels.
Waste Reduction and Resource Management
- Building in a factory cuts down waste by up to 50% compared to traditional methods.
- Factory settings also mean better resource management, less health risks, and less harm to the environment.
Green Building Practices
Prefab construction follows green building rules. It uses eco-friendly materials, renewable energy, and designs for natural light and air. These steps help make prefabricated workforce housing more sustainable.
Prefabrication helps construction projects be kinder to the planet. It includes energy-saving, waste-cutting, and green building practices. These make modular worker housing a smart, green choice for the construction world.
Quality Control and Construction Standards
Quality control is key in site housing and prefab worker colonies. The prefab process is closely watched at every step. This ensures top-notch quality, better than traditional building methods.
The factory setting helps keep dimensions and tolerances precise. This leads to better quality control. Prefab buildings meet strict standards, ensuring they are safe and strong.
- By 2025, it is expected that prefabricated buildings will constitute 30% of all new building space in China.
- The prefabricated building industry is currently dealing with issues such as weak quality assurance systems, lack of standardization in construction organization and administration, and insufficient professionalism among construction employees.
- Zhang et al. utilized ISM-BN to establish an evaluation model for factors affecting the quality of as-assembled structures in prefabricated buildings.
- Xia et al. examined quality criteria during the manufacturing, shipping, storage, and lifting stages of prefabricated structures.
Top manufacturers like SAMAN Portable focus on quality. They ensure their site housing and prefab solutions meet high standards. This makes them stand out in the industry.
Prefabricated labor sheds save time and reduce waste. They are also cost-effective. SAMAN Portable is known for its quality, versatility, and eco-friendly solutions. They serve construction projects nationwide.
Worker Welfare and Living Conditions
Modern prefab labor colonies focus on worker welfare in prefab housing and living conditions. They aim to make the workforce happy and healthy. Happy workers lead to better productivity and project success.
Comfort and Amenities
Prefab employee accommodation is built with workers in mind. These modules have big, airy living spaces for privacy and comfort. They include beds, storage, and common areas for a nice living space.
Health and Hygiene Facilities
Health and hygiene are key in these prefabricated site camps. They have modern sanitation like clean water, toilets, and baths. There are also medical clinics and first-aid stations for on-site healthcare.
Community Spaces and Recreation
- Shared spaces in the cost-effective labor housing help workers bond and feel part of a community.
- Recreational areas like sports courts, fitness centers, and leisure zones help workers stay active and relaxed.
These on-site labor housing solutions meet workers’ needs and improve their lives. They aim to make workers happy, productive, and loyal. This helps large-scale projects succeed.
Installation Process and Site Preparation
Building modern industrial labor housing and worker colonies is now faster thanks to prefab designs and prefabricated workforce shelters. The setup for these new solutions shows how far modular construction has come.
Getting the site ready is key for the long-term strength and smooth fit of prefab labor colonies. A detailed soil check is done to figure out the best foundation. This careful planning makes the setup process smooth, avoiding future problems.
- Factory-controlled making of pre-engineered parts
- Quick transport and logistics to the site
- Easy on-site assembly needing little labor
- Weather-safe setup, cutting down on delays
- Thorough site prep, including foundation and utility setup
The prefab method cuts down on time and resources needed for old-school building. Up to 90% of the work is done off-site. This leads to a quick and efficient setup. It also means better quality and consistency in the building process.
With good site prep and the benefits of modern prefab labor camp solutions, builders and developers can create top-notch worker colonies. These meet the workforce’s needs while saving time, resources, and money.
Maintenance and Long-term Management
Keeping prefabricated labour colonies in good shape is key to their long-term success. Unlike traditional buildings, prefab solutions need less upkeep. This is because they are built in factories and assembled on-site.
Regular Upkeep Protocols
Regular checks and maintenance are vital for prefab homes. Inspections help spot and fix problems early. This keeps the homes in top condition.
Repair and Replacement Strategies
The modular design makes repairs easy. Parts can be swapped out quickly. This keeps the homes running smoothly with little downtime.
Life Cycle Assessment
Studies show prefab homes can last a long time. With the right care, they often outlive their expected lifespan. This makes them a valuable and sustainable option.
Regular maintenance, smart repairs, and a focus on the whole life cycle help prefab homes last. They stay energy-efficient and functional for years. This makes them a reliable and sustainable choice for India’s workforce.
Regulatory Compliance and Permissions
When using modular construction for worker accommodation, temporary shelters, and rapid deployment projects, following rules is key. Prefab buildings must meet strict local, state, and international building codes. This ensures safety and follows the law.
In the United States, modular buildings follow the International Building Code (IBC). But, rules can differ by state. Getting the right permits, like building and utility permits, is vital before starting. Inspections by third parties are also needed to check if everything meets the rules.
It’s important to know and follow these rules for prefab labour colonies. This might mean dealing with many local, state, and federal laws. But, it’s a must for creating safe and legal places for workers. By being well-informed and managing compliance well, companies can smoothly set up their modular projects.
- Compliance with International Building Code (IBC) guidelines
- Obtaining necessary permits, including building, utility, and occupancy permits
- Undergoing third-party inspections to verify compliance
- Understanding and adhering to local, state, and federal regulations
- Proactive management of the compliance process for a smooth deployment
Future Trends in Modern Prefab Labour Colonies
The construction industry is changing fast. Modern prefab labour colonies are getting a boost from new tech and market needs. These changes will make building homes and managing workers more efficient and cost-effective.
Technological Advancements
Building Information Modeling (BIM) is becoming more popular in prefab labour colonies. BIM helps with better design, project management, and off-site building. This leads to more sustainable design and cost-effective housing.
Smart Integration Features
Modern prefab labour colonies are getting smarter. They use IoT devices for better energy use, security, and comfort. These smart integration features make prefab colonies more efficient and comfortable for workers.
Emerging Market Demands
There’s a big push for eco-friendly and sustainable construction. Prefab labour colonies fit right into this trend. Their off-site fabrication and use of new materials cut down on waste and save energy. As the focus on sustainability grows, so will the demand for prefab labour colonies.
Technological progress, smart features, and market needs are changing prefab labour colonies. By adopting these innovations, builders can offer sustainable design, off-site fabrication, cost-effective housing, and workforce management. This leads to efficient and adaptable living solutions for projects.
Conclusion
Modern prefab labour colonies are a great solution for worker housing in India and worldwide. They are efficient, cost-effective, and sustainable. This meets the needs of employers and workers alike.
The future of prefab construction in labor housing looks bright. New technologies and a focus on sustainability are driving progress. This makes prefab a key player in the construction industry.
Prefab solutions are essential for quick, quality, and affordable worker housing. They are low-cost, fast to build, and can be reused. This makes them a popular choice for construction projects.
In the United States, prefab buildings follow the International Building Code. India is also adopting similar standards. This ensures prefab buildings are safe and meet building codes.
Prefabricated construction materials are getting better at being sustainable and durable. They use less material and energy than traditional methods. As housing and office needs grow, prefab structures are being improved. Digital tools like Building Information Modeling (BIM) help with assembly.
FAQ
What is prefabricated construction, and how does it differ from traditional construction?
Prefabricated buildings, or prefabs, are made in a factory and then put together at the site. This method is more efficient than building on-site because it happens in a controlled environment.
How has the concept of prefabrication evolved over time?
Prefabrication started with nomadic people needing easy-to-move shelters. It grew during colonization and really took off in the 20th century, especially during and after World Wars.
What are the key components and manufacturing processes involved in prefab construction?
Prefab structures include walls, roofs, and floors made off-site. Modern methods use shop welding and precast concrete to make production efficient.
What are the main benefits of prefabricated labour colonies in India?
Prefab buildings in India are becoming popular for their efficiency and cost-effectiveness. They are faster, of higher quality, and can be customized to meet the need for quick, affordable worker housing.
What design considerations are important for prefab labour colonies?
Designing prefab labour colonies focuses on space, layout, and durable materials. Safety and following standards are key, with strict inspections during manufacturing.
What are the economic benefits of prefabricated construction?
Prefab construction saves time and money. While it might cost a bit more at first, it’s faster. This saves on labor and on-site costs, leading to overall savings.
How does prefab construction address environmental impact and sustainability?
Prefab construction is green because it uses materials and energy wisely. It reduces waste and uses energy-efficient designs, lowering its carbon footprint.
How is quality control maintained in prefab construction?
Quality control in prefab is strict, with checks at every step. This ensures higher quality and consistency, thanks to factory settings.
What features are prioritized in modern prefab labour colonies to improve worker welfare?
Modern prefab labour colonies focus on worker comfort and well-being. They include amenities, health facilities, and community spaces to boost satisfaction and productivity.
What is the installation process for prefab labour colonies, and what are the key considerations?
Installing prefab labour colonies involves site prep and assembling components. Assessing the site, including soil type, is critical for the structure’s durability and longevity.
How are prefab buildings maintained, and what are the long-term management strategies?
Maintaining prefab buildings is easier due to their durable materials and precise manufacturing. Regular upkeep and repair strategies are key to their long life.
What are the regulatory requirements for prefabricated labour colonies?
Prefab buildings must meet local, state, and international building codes. Getting permits and undergoing inspections ensures they comply with all regulations.
What are the emerging trends and future developments in the field of prefab labour colonies?
Future trends include prefab housing trends using advanced technologies like BIM and smart features. The focus is on sustainable design and materials to meet the demand for quality, affordable worker housing.