Comprehensive Guide to PEB Building Design and Structure: Key Elements, Safety, and Durability
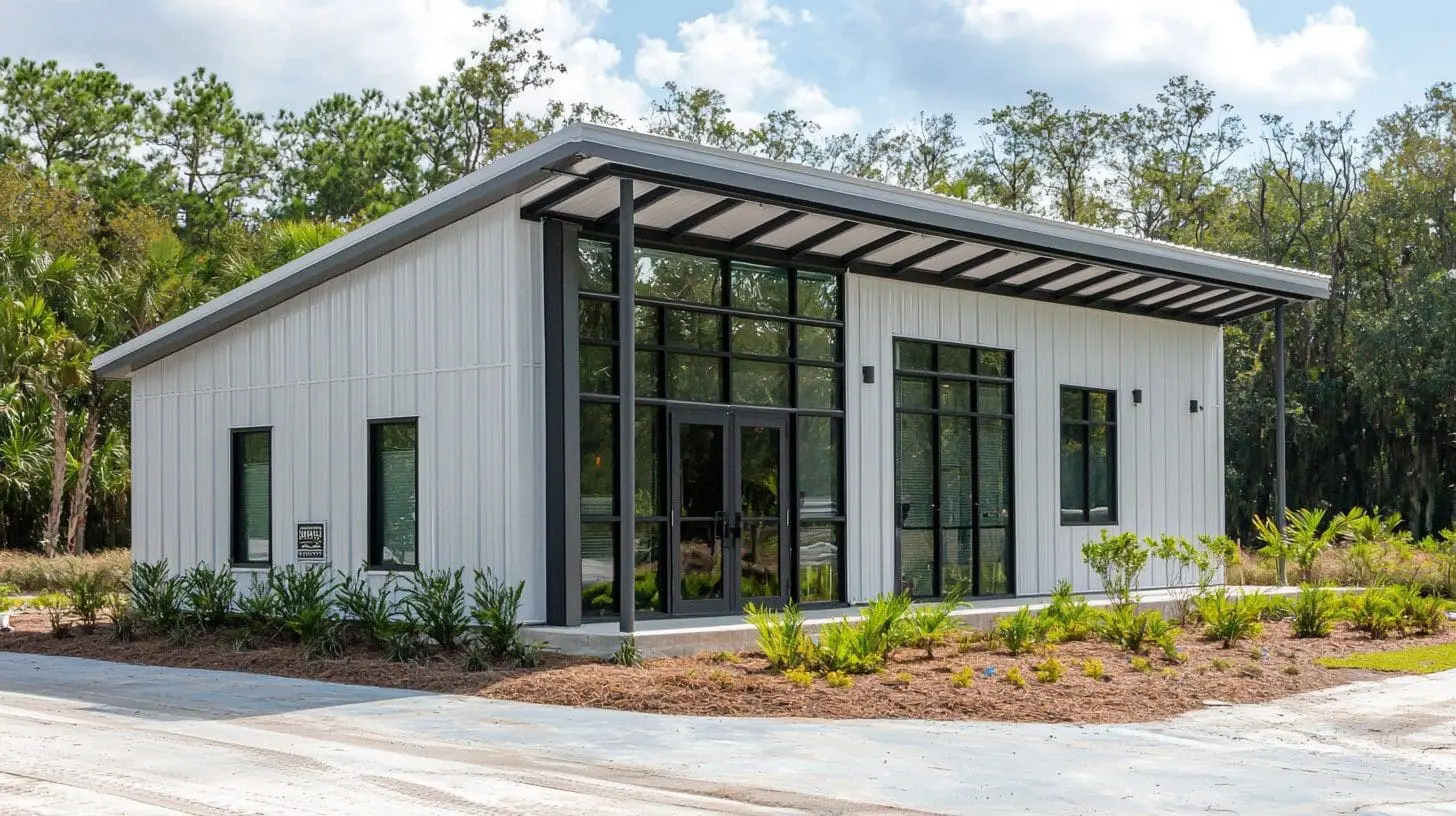
Introduction to Design of PEB Structure
Understanding PEB Building Design
Pre-engineered buildings (PEBs) have become an integral part of modern construction, thanks to their cost-effectiveness, speed, and adaptability. PEB structures are developed with a focus on prefabrication and modular construction, making them efficient and highly customizable for various industrial, commercial, and residential needs. Unlike traditional buildings, PEBs are engineered in a factory and then assembled on-site, allowing for rapid construction while maintaining strict quality standards. This approach not only streamlines the process but also ensures that each component of the PEB structure is designed for optimal durability and safety.
The design of a PEB structure involves careful planning and consideration of factors such as the building’s intended use, site-specific conditions, and structural load requirements. Each element, from the frame to the cladding, is chosen to provide maximum strength and stability, making PEBs a popular choice for businesses seeking a cost-effective yet robust solution for large-scale facilities. Pre-engineered metal structures are commonly used for warehouses, factories, and agricultural buildings due to their adaptability and efficiency.
Why Choose PEBs Over Traditional Construction?
The key advantage of PEB structures lies in their modularity and factory-based production. While traditional construction often requires on-site fabrication and extended labor, PEBs are built using pre-manufactured components that are delivered to the site for quick assembly. This not only reduces construction time but also minimizes waste, aligning with sustainable construction practices. For instance, modular portable cabins and container-based structures are widely used in industries that need temporary or portable solutions.
Applications of PEB Building Designs
PEBs are adaptable to various applications, from expansive warehouses to compact prefabricated units used as office spaces or residential housing. Their flexibility allows PEBs to cater to specific needs, whether it’s a large, column-free interior for industrial equipment or a modular setup for portable offices. The design can be tailored with features such as insulated panels, ventilation systems, and durable coatings to protect against environmental factors. These customizations make PEBs versatile enough for use across industries, from logistics to education, where they can serve as schools, porta cabins, or emergency shelters.
Conclusion
The unique design and structural approach of PEBs make them a go-to choice for modern construction needs. With features that support both durability and customization, PEBs offer a practical solution that stands up to various demands. In the following sections, we’ll delve deeper into the structural elements and engineering considerations that give PEB buildings their strength and reliability.
To appreciate the full spectrum of advantages offered by PEB buildings, explore our PEB Buildings Benefits, Features & Applications page for an in-depth analysis.
Design Considerations in PEB Structures
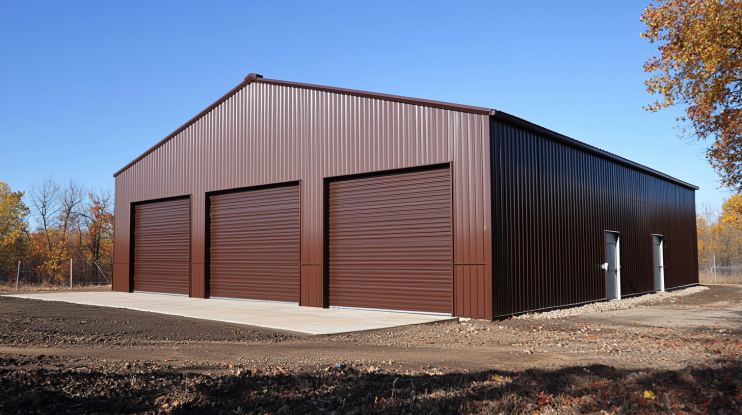
Essential Factors Influencing PEB Design
The design of pre-engineered building (PEB) structures involves a meticulous approach to ensure durability, safety, and functionality. Unlike conventional buildings, where designs may be adapted to suit individual aesthetics, PEBs prioritize structural integrity and modular efficiency. Several crucial factors come into play when designing a PEB structure, such as environmental conditions, load-bearing requirements, and building codes, each of which significantly impacts the building’s stability and lifespan.
PEB design begins with an in-depth assessment of the site’s geographical location and climate. Factors like wind speed, temperature extremes, and seismic activity are considered to determine the building’s resilience under specific environmental stresses. Engineers account for these site-specific conditions to reinforce the structure where necessary, ensuring that the PEB is not only stable but also optimized to withstand environmental challenges. This attention to location is essential for structures like portable industrial cabins and temporary modular units used in diverse environments.
Load Factors and Safety Standards
Another critical aspect of PEB structure design is load calculation. Engineers must carefully evaluate the loads the building will bear, including dead loads (permanent structural weight), live loads (temporary weight from people, equipment, etc.), and dynamic loads from wind or seismic forces. Proper load distribution is crucial in preventing structural failure and ensuring the building’s safety over time. For instance, PEB warehouses require an open layout with strong load-bearing capacity to accommodate storage racks and heavy equipment. The use of pre-fabricated steel components allows PEBs to handle substantial loads without sacrificing flexibility.
Adhering to building codes and safety regulations is a non-negotiable part of PEB design. Codes vary based on region, but they are essential to ensure the safety and stability of engineered buildings. Compliance with these standards guarantees that the building can handle its intended load and environmental stresses. Many engineered steel buildings integrate additional safety features to meet or exceed regulatory requirements, making them suitable for industries that require robust safety protocols.
Modular and Site-Specific Design
The modular design of PEBs allows for easy adaptation to specific site needs, whether for permanent installations or portable structures. This flexibility enables businesses to expand or modify buildings as their needs change. Many PEB structures are crafted with adjustable features, such as extendable frames or replaceable wall panels, enabling companies to customize their facilities without extensive reconstruction. In applications like modular container offices or portable cabins, modularity offers an efficient solution to meet immediate needs with the option for future adjustments.
Conclusion
The design considerations for PEB structures ensure they can withstand environmental and operational demands. By addressing location, load factors, and compliance with safety standards, PEB designs deliver stable, adaptable structures that meet diverse industry needs.
Ensure your design vision is executed flawlessly by partnering with top-tier manufacturers. Visit our PEB Building Manufacturers in India to connect with industry leaders.
Components of a Pre-Engineered Building Structure
Key Elements of PEB Structures
Pre-engineered building (PEB) structures are composed of several core components designed for durability, functionality, and ease of assembly. Each component plays a vital role in the building’s stability, strength, and adaptability to various applications. The primary components of a PEB structure include the main frames, secondary members, roof and wall claddings, and various accessories. This modular design ensures that PEBs are versatile and can be adapted to fit different industrial, commercial, and even residential requirements.
The main frames, made from steel, serve as the primary load-bearing elements of the structure. These frames are precision-engineered to provide a strong and stable foundation, with each frame supporting the weight of the building and any additional loads. The steel used in these frames is often treated with protective coatings to prevent corrosion, which is essential for maintaining structural integrity over time. Industries that require robust and resilient structures, such as industrial manufacturing facilities, rely on the strength of these frames to support heavy equipment and large storage systems.
Secondary Members and Their Role
The secondary members, which include purlins, girts, and bracings, work alongside the main frames to reinforce the structure and provide additional support. Purlins and girts help distribute loads evenly across the building, reducing stress on the primary frames. These members also play a crucial role in supporting the roof and wall cladding, which protects the interior from weather conditions. This combination of primary and secondary components results in a stable and balanced structure, which is particularly beneficial for storage buildings that need open layouts and maximum internal space.
Roof and Wall Cladding for Protection and Insulation
Roof and wall claddings are essential for protecting the building from external elements. These claddings are often made from materials like steel or aluminum, providing a durable shield against wind, rain, and temperature fluctuations. The choice of cladding can vary depending on the building’s location and intended use. For instance, a portable warehouse unit may use insulated wall panels to ensure temperature control, while industrial units may opt for metal cladding for enhanced durability. Some PEBs even incorporate energy-efficient cladding to minimize heat transfer, helping to keep the building interior comfortable and reducing energy costs.
Accessories and Customizable Features
PEBs can also be equipped with various accessories that enhance functionality and appearance. These accessories may include ventilation systems, skylights, windows, doors, and insulation. Customizable features allow businesses to adapt their PEBs to meet specific requirements, whether it’s adding extra ventilation in a manufacturing unit or installing soundproofing in modular office cabins. Such customization makes PEBs versatile and suitable for a range of purposes, including temporary offices, storage facilities, and more.
Conclusion
The components of a PEB structure work together to provide a reliable and efficient building solution. By combining strong frames, supportive secondary members, and durable cladding, PEBs deliver stability, protection, and adaptability for various industries.
Transform your residential projects with expert design strategies. Our articles on Prefabricated Houses in Hyderabad and Prefabricated Houses in Kerala showcase practical applications of PEB structures.
Structural Safety and Load-Bearing Considerations
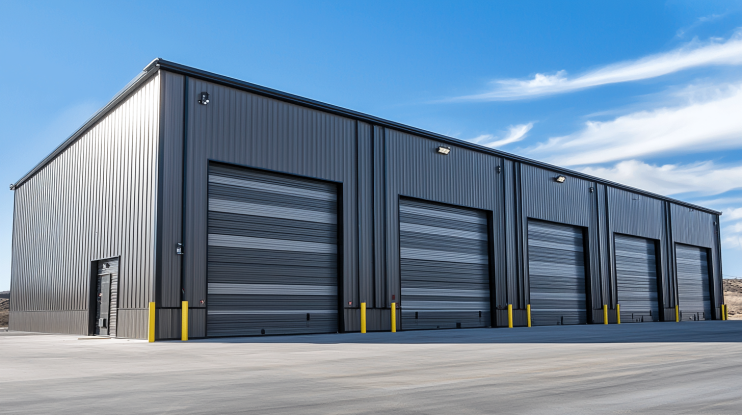
Understanding Load Types in PEB Design
One of the defining features of pre-engineered buildings (PEBs) is their ability to manage various types of loads while maintaining structural integrity. In PEB design, engineers must carefully assess and accommodate different load types: dead loads, live loads, and environmental loads like wind and seismic forces. Dead loads refer to the building’s permanent weight, including structural components, while live loads account for temporary weight from people, equipment, or inventory. Environmental loads vary depending on location and can include factors like snow accumulation, high winds, and earthquakes. Calculating these loads is crucial to ensuring that the PEB structure can endure specific stresses without compromising safety.
By engineering the building to handle these loads effectively, PEB structures offer safety and reliability in various applications, from temporary storage units to large industrial warehouses. For instance, in locations with high snow loads, roofs may be reinforced to prevent collapse, while buildings in seismic zones might include bracing systems for additional stability.
Importance of Load-Bearing Components
PEB structures utilize primary and secondary load-bearing components to distribute weight efficiently across the building. The primary frames, which consist of rigid steel columns and rafters, bear the majority of the structural load. These frames are designed to provide the building with core stability, ensuring that it remains stable under heavy loads and adverse conditions. Secondary members, such as purlins and girts, help transfer the weight from the cladding to the main frames, adding an additional layer of support.
These load-bearing elements are engineered to provide optimal stability, which is essential for high-capacity warehouses that rely on open floor space and column-free interiors. By efficiently distributing loads through both primary and secondary components, PEBs can achieve a stable and balanced structure that meets various industrial requirements.
Safety Standards and Building Codes
Adhering to regional building codes and safety standards is a fundamental aspect of PEB design, particularly when it comes to load-bearing requirements. Engineers ensure that each PEB meets or exceeds local safety standards, which vary based on geographic and environmental factors. These regulations often require specific load tolerances and safety features that align with local conditions, such as wind resistance in hurricane-prone areas or extra structural reinforcement in earthquake zones. Many custom-engineered metal buildings integrate specialized features to meet industry-specific regulations, providing a safe and compliant structure for various applications.
Structural Reinforcements for Extreme Conditions
For PEBs installed in regions subject to extreme weather, structural reinforcements are often included to improve resilience. For example, buildings in high-wind areas may incorporate reinforced bracing or heavier steel frames to prevent collapse. Similarly, PEBs used as container-based structures in coastal areas might feature corrosion-resistant coatings to protect against saltwater exposure. These reinforcements extend the building’s lifespan and ensure that it can operate safely under challenging conditions.
Conclusion
The load-bearing and safety considerations in PEB design are key to delivering a stable and secure building. Through rigorous load analysis, structural reinforcements, and adherence to safety standards, PEBs are engineered to provide durability and protection across a wide range of applications.
Stay updated with the latest innovations in prefab housing by reading our Prefabricated House in Pune Overview. Discover new techniques and designs that push the boundaries of construction.
Key Elements in PEB Design for Durability
Material Selection for Long-Lasting Structures
Durability is a primary focus in the design of pre-engineered buildings (PEBs), and material selection plays a pivotal role in achieving this longevity. Most PEB structures are constructed using high-quality steel, which is not only strong but also adaptable to various environmental conditions. Steel provides excellent load-bearing capabilities, making it an ideal choice for industries that require resilient buildings, such as modular industrial facilities. To further enhance durability, steel used in PEBs is often treated with protective coatings to resist corrosion, ensuring the structure remains intact even in harsh weather.
For buildings exposed to moisture or corrosive environments, additional treatments like galvanization or specialized coatings are applied to the steel surfaces. These coatings create a barrier that prevents rust and deterioration, extending the life of the structure. For example, prefabricated storage units often incorporate galvanized steel to withstand humidity and temperature fluctuations, providing a long-lasting solution for various storage needs.
Weather-Resistant Design Features
PEBs are often deployed in diverse climates, requiring thoughtful design features to ensure they remain structurally sound. Weather-resistant design elements, such as sloped roofing and reinforced joints, are integrated to protect the building from wind, rain, and snow. Sloped roofs, for instance, allow rain and snow to slide off easily, reducing the potential for accumulation that could otherwise lead to structural strain. In regions prone to high winds, additional bracing is included to enhance stability and prevent movement, making PEBs a reliable option for temporary site accommodations and other industrial structures.
Insulation is another essential element in PEB durability, especially for buildings that require consistent internal temperatures, such as warehouses or office units. Insulated panels or wall claddings help regulate internal temperatures, improving energy efficiency and protecting the building’s structural elements from expansion and contraction due to extreme temperatures. This thermal protection helps maintain the integrity of components over time, supporting the long-term durability of PEBs in challenging environments.
Low-Maintenance Requirements
PEBs are designed to require minimal maintenance, a feature that contributes significantly to their longevity and cost-effectiveness. The use of durable materials like treated steel means that the building’s exterior is largely self-sustaining, reducing the need for frequent repairs. Unlike traditional structures that may suffer from issues like peeling paint, PEBs avoid such problems due to their corrosion-resistant coatings and robust materials. This low-maintenance quality is particularly appealing for portable and modular buildings that may be relocated or used in temporary settings.
Structural Reinforcements for Added Strength
PEBs are often reinforced with bracing and other structural supports to handle specific operational demands. Cross-bracing is commonly used to improve resistance against lateral forces, such as those caused by wind or seismic activity. Additionally, heavy-duty frames are used in buildings that will support large machinery or high-capacity storage, ensuring the structure can handle substantial internal forces. These reinforcements make PEBs a versatile choice for applications requiring both durability and strength, whether it’s a modular storage unit or an industrial workspace.
By incorporating durable materials, weather-resistant designs, and low-maintenance requirements, PEBs provide a reliable building solution capable of withstanding various operational and environmental challenges.
Optimize your farm housing projects with insights from our Prefab Farm Homes India Guide. Learn how to create efficient and sustainable farm homes using PEB structures.
Advantages of Engineered Structures
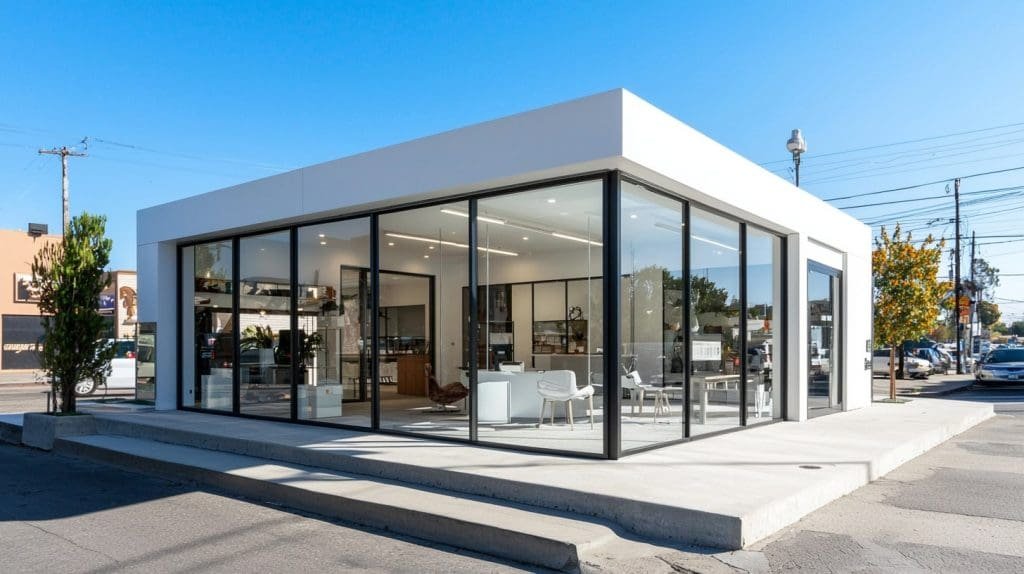
Cost-Effectiveness and Resource Efficiency
Engineered structures like pre-engineered buildings (PEBs) are designed with cost efficiency in mind, making them a financially viable choice for businesses seeking durable yet economical construction solutions. PEBs leverage prefabrication and modular assembly, which significantly reduces labor costs and construction time. Unlike traditional building methods, which often face delays and high expenses due to on-site customization, PEBs are pre-manufactured in factories to exact specifications. This efficiency allows businesses to save on resources while maintaining high-quality standards, especially beneficial for projects that require quick setups, like modular storage facilities and temporary warehouses.
Beyond initial savings, PEBs offer long-term financial benefits through their low-maintenance design. With materials like treated steel, which resists corrosion and wear, PEBs require fewer repairs and upkeep over the years. This cost-saving advantage makes them appealing for industries looking to reduce operational expenses while investing in a reliable building structure.
Time-Saving Benefits
One of the key advantages of PEBs is the reduction in construction time. Because these buildings are fabricated off-site and then assembled on-site, PEBs can be installed within weeks, rather than the months or years typical of conventional construction. This rapid timeline is advantageous for businesses that need operational facilities on short notice, such as portable office buildings for project sites or pop-up retail spaces.
In emergency scenarios or industries with fluctuating demand, PEBs provide a quick and efficient solution, enabling companies to establish functional spaces without prolonged lead times. The modular nature of PEBs also allows for easy expansion if additional space is required, making them a flexible choice for growing businesses.
Environmental Sustainability
PEBs are recognized as a sustainable building option, aligning with eco-friendly practices that reduce construction waste and energy consumption. Factory-based prefabrication minimizes on-site waste, and the materials used in PEBs, such as recyclable steel, support the goal of sustainable resource use. Additionally, PEBs can be designed with energy-efficient elements like insulated panels and solar-ready roofing, which help reduce energy costs over time.
The environmental benefits of PEBs make them suitable for businesses aiming to meet green building standards and reduce their carbon footprint. For instance, modular office cabins and container-based units can be outfitted with insulation and energy-efficient lighting, creating an eco-friendly workspace that supports sustainability initiatives.
Versatility Across Industries
PEBs are highly versatile, serving multiple industries such as manufacturing, retail, agriculture, and logistics. Their adaptable design allows them to be customized for various uses, from industrial storage spaces to agricultural barns. Because PEBs are engineered to meet specific requirements, they can easily accommodate diverse operational needs. This adaptability has led to the widespread adoption of PEBs for both permanent and temporary structures, demonstrating their suitability for various sectors.
Engineered structures like PEBs are especially advantageous for industries needing scalability and adaptability, allowing businesses to invest in spaces that can grow and evolve alongside their operations.
Elevate your construction projects with advanced methods outlined in our Precast Housing Construction Guide. Discover the benefits of precast technology in modern building.
Customization and Flexibility in PEB Design
Tailoring PEB Structures to Specific Needs
One of the most appealing aspects of pre-engineered buildings (PEBs) is their remarkable flexibility in design and customization. Unlike traditional construction, which can be rigid and difficult to modify, PEBs allow for a high degree of adaptability to meet specific functional and aesthetic requirements. Whether used for warehouses, offices, or industrial spaces, PEB structures can be customized in various ways, from layout adjustments to finishes and specialized features. This versatility is particularly useful for businesses needing custom-built modular storage units or temporary office spaces that cater to specific operational needs.
PEB customization begins at the planning stage, where businesses can select structural layouts, roofing styles, and wall finishes based on their industry requirements. For instance, open floor plans are commonly chosen for warehouse facilities to maximize storage capacity, while partitioned layouts are ideal for modular offices. Each component, from wall cladding to interior dividers, can be adjusted to ensure that the final structure aligns with the intended use and aesthetic goals.
Functional Features for Enhanced Usability
Beyond the basic layout, PEBs can incorporate various functional features that improve usability and meet industry standards. Elements like insulation, soundproofing, climate control, and ventilation systems can be added to ensure comfortable and efficient operations. For example, modular office cabins are often customized with insulated walls and air conditioning systems to provide a productive environment for staff, even in extreme climates.
Additionally, PEBs can include advanced lighting solutions, fire safety systems, and energy-efficient windows to enhance operational efficiency. These features allow PEBs to serve specialized needs, such as climate-controlled environments for storage facilities or soundproofed spaces for industrial operations. The ability to add or modify functional elements offers businesses a high level of control over their building’s performance, making PEBs an attractive choice for diverse applications.
Adaptability for Future Expansion
PEBs are also designed with future scalability in mind, a feature that distinguishes them from more conventional structures. Modular components and flexible layouts make it easy to expand or reconfigure the building as needed. For businesses expecting growth, PEBs offer the option to add additional units or expand existing spaces without disrupting current operations. This adaptability is particularly valuable for industries such as manufacturing and logistics, where space needs may evolve over time. For instance, container-based modular facilities can be expanded by adding more containers, allowing businesses to increase capacity quickly and affordably.
Aesthetic Customization for Brand Alignment
In addition to functionality, aesthetic customization options are available for PEBs, allowing businesses to align their building’s appearance with their brand identity. Options such as color finishes, architectural facades, and custom signage can give PEBs a distinct look, enhancing the company’s image. This level of customization is beneficial for retail spaces, offices, and customer-facing facilities where brand presentation is important. Many portable office buildings now incorporate stylish exteriors and modern finishes to create an appealing, professional appearance.
The customization and flexibility of PEBs make them a practical and attractive solution for businesses seeking both form and function. By tailoring each aspect of the structure, companies can create spaces that meet their current demands while allowing for future growth and changes.
Implement effective urban housing strategies by consulting our Prefab Homes Mumbai Guide. Tailor your designs to meet the unique demands of Mumbai’s urban environment.
Sustainability in PEB Structure Design
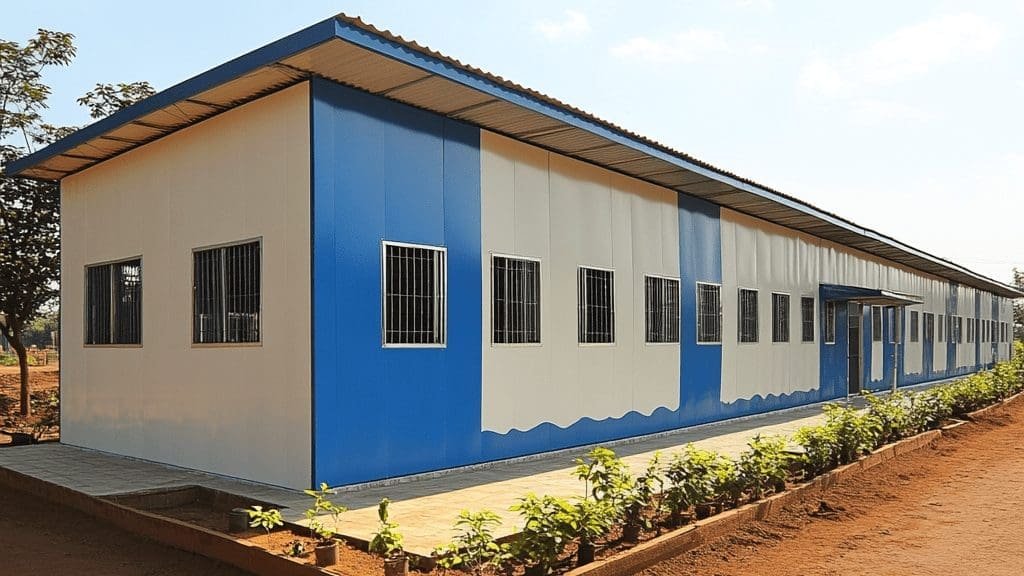
Eco-Friendly Materials and Resource Efficiency
Sustainability is becoming a priority in the construction industry, and pre-engineered buildings (PEBs) align with eco-friendly practices through their design and material choices. PEBs primarily use recyclable materials like steel, which not only provides strength but also supports sustainable construction practices. Steel is known for its recyclability, meaning that PEB components can be reused or repurposed at the end of their life cycle, reducing environmental impact. This makes PEBs an ideal choice for industries looking to minimize waste while building durable structures, such as prefabricated storage solutions and temporary workspaces.
PEBs are also resource-efficient due to their prefabrication process. Since components are manufactured off-site in controlled environments, waste is minimized during production. Additionally, precision manufacturing ensures that each part of the building is produced accurately, reducing the need for excess materials. The factory-controlled production of PEBs results in a lean construction process that produces less waste compared to traditional methods, making PEBs a more sustainable building option overall.
Energy Efficiency Through Insulation and Design
Energy efficiency is a core element of sustainable design, and PEBs can be outfitted with features that reduce energy consumption. Insulation options, such as insulated wall panels and roofing systems, help regulate indoor temperatures, making PEBs more energy-efficient and cost-effective. Proper insulation reduces the need for heating and cooling, thereby lowering energy costs and the building’s overall carbon footprint. This is especially beneficial for modular office buildings and other commercial PEB structures that operate year-round.
In addition to insulation, PEBs can be designed with energy-saving lighting solutions, such as LED lights and skylights that reduce the need for artificial lighting during the day. Skylights and windows can also improve ventilation, which is crucial in maintaining indoor air quality and reducing reliance on HVAC systems. These design features contribute to a comfortable interior while keeping energy demands low, supporting the goal of reducing environmental impact.
Renewable Energy Integration
As renewable energy sources become more accessible, PEBs are increasingly integrating technologies like solar panels to further enhance sustainability. Roof-mounted solar panels can be installed on PEBs to generate clean, renewable energy, reducing dependence on grid electricity and lowering operational costs. Solar-ready roofing systems are an attractive option for container-based modular structures and other temporary or semi-permanent buildings, allowing businesses to operate sustainably even in remote or off-grid locations.
Renewable energy integration is particularly valuable for industries that prioritize eco-friendly operations, as it aligns with global efforts to reduce greenhouse gas emissions. By designing PEBs with sustainability in mind, businesses can lower their carbon footprint and contribute to a greener future.
Alignment with Green Building Standards
PEBs can also be designed to meet green building certifications and standards, such as LEED (Leadership in Energy and Environmental Design), which promote sustainable construction practices. By incorporating energy-efficient materials, eco-friendly features, and renewable energy sources, PEBs are capable of meeting stringent environmental standards. These certifications not only benefit the environment but can also enhance a company’s reputation as a responsible and sustainable business. Portable modular offices, for example, can be customized with energy-saving features that align with sustainability objectives, appealing to eco-conscious clients and customers.
Through sustainable materials, energy efficiency, and renewable energy options, PEBs support the construction industry’s shift toward greener building solutions. This focus on sustainability ensures that PEBs are not only durable and versatile but also environmentally responsible, meeting the needs of businesses aiming to reduce their environmental impact.
Commit to sustainable design by integrating used materials. Our Used Containers for Sale in Chennai page offers innovative solutions for eco-friendly construction.
Future Trends in PEB Building Design
Advancements in Material Science for Enhanced Durability
As technology advances, material science is playing an increasingly important role in the future of pre-engineered building (PEB) design. New materials, such as high-strength alloys and corrosion-resistant coatings, are being developed to improve the longevity and resilience of PEB structures. These innovations allow PEBs to withstand extreme environmental conditions, making them suitable for both industrial and commercial applications. Many modular industrial units are now incorporating these advanced materials to ensure that they can handle demanding environments while maintaining structural integrity over the long term.
Another exciting development is the use of self-healing materials, which are designed to repair minor damage on their own. This can significantly reduce maintenance costs and extend the lifespan of PEB structures, especially in harsh environments. These advancements mean that PEBs are becoming even more robust and reliable, aligning with the demands of modern construction.
Integration of Smart Technology in PEBs
The future of PEB structures is also seeing a shift towards “smart” technology. Integrating Internet of Things (IoT) devices within PEBs allows for real-time monitoring of structural integrity, energy usage, and environmental conditions. Sensors can be installed in critical areas of the building to track load stress, temperature, humidity, and even vibration levels. This data is invaluable for industries that operate heavy machinery, as it enables proactive maintenance and reduces the risk of unexpected structural failures. IoT integration is particularly beneficial for containerized modular spaces used in remote or industrial settings, where regular monitoring can help extend the building’s functionality and safety.
With smart technology, PEBs can also be automated to control lighting, heating, and ventilation, thereby enhancing energy efficiency and reducing operational costs. This technology is rapidly transforming the construction landscape by creating intelligent buildings that adapt to environmental and operational needs in real time.
Focus on Modular Multi-Story PEBs
As urbanization increases, the demand for multi-story PEBs is growing. Multi-level modular PEBs offer an efficient solution for urban areas with limited space, providing stacked floors while retaining the efficiency and speed of PEB construction. Unlike traditional multi-story buildings that require extensive on-site construction, modular multi-story PEBs can be assembled in sections, which are then stacked and secured. This modularity makes them a practical option for commercial offices, hotels, and multi-level warehouses. Portable office cabins and other modular workspaces can benefit greatly from this design, offering flexible spaces that can be expanded vertically without disrupting nearby structures.
Sustainable and Green Innovations
The trend toward sustainability continues to influence PEB design, with green innovations being incorporated into new projects. The use of solar-ready roofing, rainwater harvesting systems, and natural ventilation designs aligns with the global push for eco-friendly construction. Some PEBs are even incorporating green roofs, which add vegetation to the building’s roof structure, reducing heat absorption and enhancing biodiversity. These sustainable innovations make PEBs a preferred choice for businesses looking to meet environmental regulations and achieve green building certifications.
With the addition of sustainable and modular multi-story designs, PEBs are evolving to meet the diverse needs of urban development and environmental sustainability. The future of PEBs is bright, with technology, materials, and smart solutions making these structures even more efficient, durable, and aligned with modern construction needs.
For a complete overview of PEB design elements and their benefits, revisit our PEB Buildings Benefits, Features & Applications page. It’s an essential resource for every PEB project.
Conclusion
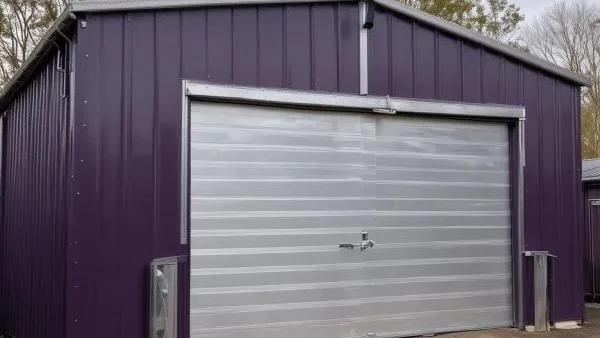
Pre-engineered buildings (PEBs) are revolutionizing the construction industry by offering fast, durable, and flexible solutions that cater to a wide range of applications. Through thoughtful design, material innovation, and a commitment to sustainability, PEBs provide cost-effective structures that are easily adaptable to diverse needs, whether they serve as industrial warehouses, modular offices, or multi-story buildings in urban spaces.
As trends in material science, smart technology, and green building continue to shape the future of PEBs, these buildings are becoming more aligned with global demands for efficiency and sustainability. PEBs are no longer just a choice for fast construction; they’re a strategic investment for businesses aiming to balance operational needs with environmental responsibility.
To learn more about our dedication to quality and innovation in pre-engineered building design, visit our About Us page for insights into our mission and services.
Frequently Asked Questions
1. What is a Pre-Engineered Building (PEB)?
A Pre-Engineered Building (PEB) is a structure designed and manufactured in a factory, then assembled on-site. It uses prefabricated components like steel frames, panels, and supports, enabling faster construction and lower costs compared to traditional building methods.
2. How is PEB different from conventional building methods?
PEBs are prefabricated and modular, which allows for quicker assembly and cost savings. Unlike conventional buildings that are built on-site from raw materials, PEBs are manufactured off-site to precise specifications, reducing waste and construction time.
3. What are the common applications of PEB structures?
PEBs are highly versatile and used across industries. They’re popular for industrial warehouses, factories, retail spaces, agricultural facilities, sports complexes, and even temporary structures like portable cabins and on-site offices.
4. What are the main benefits of using PEBs?
PEBs offer several advantages, including faster construction times, cost savings, low maintenance, energy efficiency, and customization options. They are durable, flexible, and can be expanded or modified as needed.
5. Can PEB buildings be customized?
Yes, PEBs are highly customizable. From the building’s layout and design to insulation, cladding, and functional features like HVAC systems, PEBs can be tailored to meet specific operational needs and aesthetic preferences.
6. Are PEBs environmentally friendly?
PEBs are considered eco-friendly due to their recyclable materials, energy-efficient designs, and minimal on-site waste. Features like insulation, solar panels, and energy-efficient lighting make them sustainable options in construction.
7. How long does it take to construct a PEB building?
The construction timeline varies based on the size and complexity of the building, but PEBs are typically completed much faster than traditional buildings. Most PEBs can be assembled within weeks, compared to months for conventional construction.
8. What maintenance is required for PEB structures?
PEBs are designed to be low-maintenance, especially those made with corrosion-resistant steel. Routine maintenance, like inspecting connections and cleaning, ensures long-term durability, but overall, PEBs require minimal upkeep.
9. How durable are PEB buildings in extreme weather conditions?
PEBs are engineered to withstand extreme weather conditions, including high winds, heavy snowfall, and seismic activity. Reinforced frames and specialized bracing systems enhance their durability and make them suitable for various climates.
10. Can PEBs be used for multi-story buildings?
Yes, PEBs can be designed as multi-story structures. Multi-level PEBs are becoming increasingly popular in urban areas for commercial offices, hotels, and residential buildings due to their modular construction, quick assembly, and durability.