Comprehensive Guide to Precast Housing and Construction: Affordable, Durable, and Sustainable Solutions
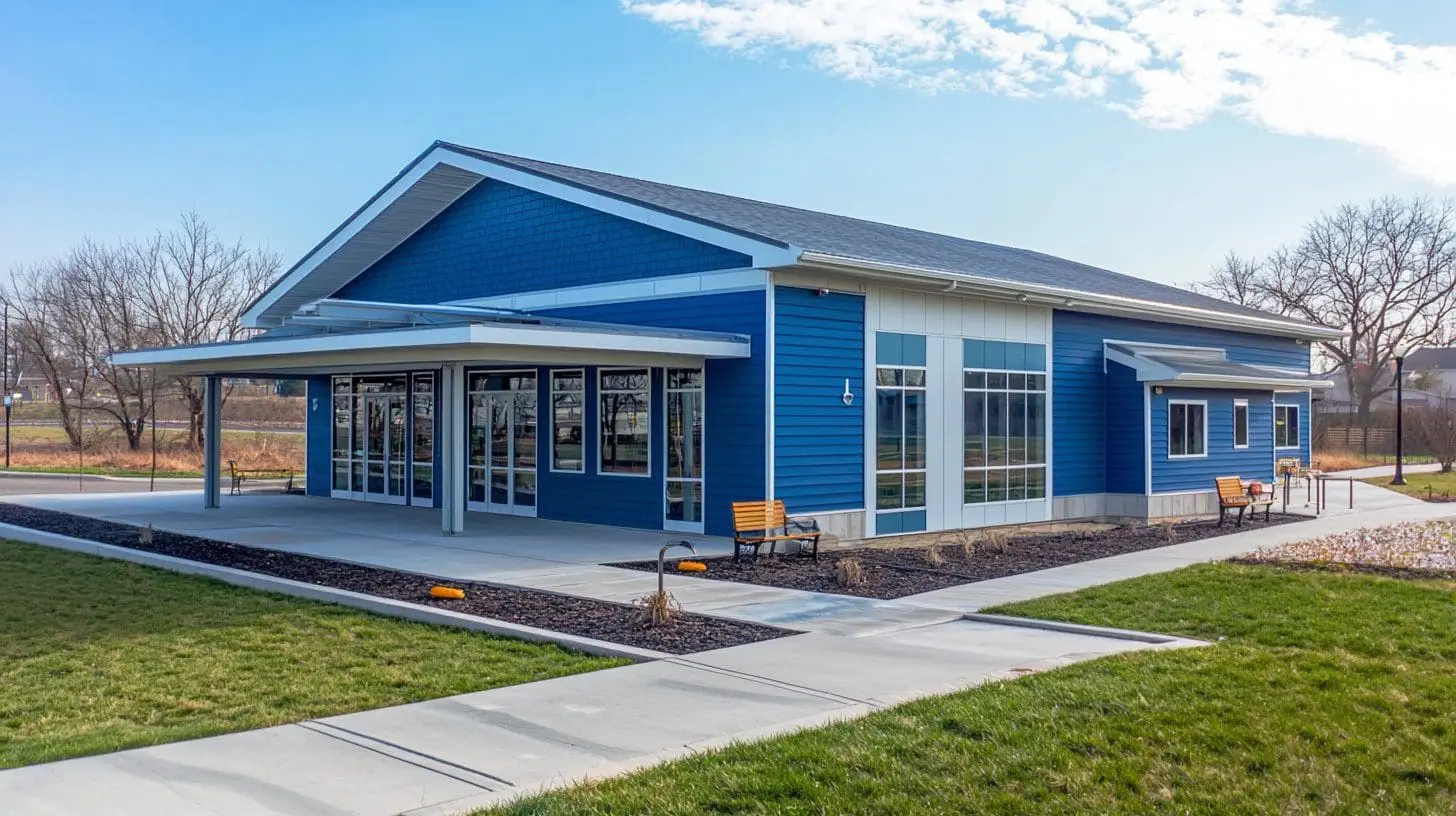
Introduction to Precast Housing and Construction
What is Precast Housing?
Precast housing is a modern construction method that involves manufacturing concrete components in a controlled factory environment before transporting them to the building site for assembly. These components, often made of high-quality precast concrete, include walls, floors, beams, and slabs, which can be quickly installed on-site to create a durable, low-maintenance, and structurally sound home. Unlike traditional brick-and-mortar construction, which takes place entirely on-site, precast housing leverages off-site production to streamline the process, reduce costs, and enhance quality control.
This approach to construction has gained popularity globally for its efficiency and cost-effectiveness, offering an alternative that is both resilient and sustainable. Precast construction also aligns with the trend toward modular and prefab building solutions, where parts of a structure are pre-manufactured to create quick, customizable building options.
Why Precast Housing is on the Rise
Precast housing is increasingly popular, especially for low-cost housing projects and high-demand urban areas where speed and affordability are crucial. As the need for rapid urbanization grows, precast concrete homes offer a way to meet housing demands without compromising on quality or durability. This technology reduces the time needed for on-site work, as the majority of the assembly happens off-site. Once the components arrive at the location, they can be assembled swiftly, making precast housing an ideal solution for projects with tight deadlines.
Additionally, the sustainability factor of precast housing makes it an appealing option for those focused on eco-friendly construction. Reduced waste, fewer on-site emissions, and the opportunity to use recycled materials contribute to precast housing’s lower environmental impact. Similar to container houses and portable cabins, precast homes minimize resource use, making them a sustainable option.
Applications of Precast Housing
Precast construction is not limited to residential projects; it has applications in commercial and industrial buildings as well. Its adaptability allows for custom layouts that meet the specific needs of residential and business environments alike. In India and many other countries, precast housing has become a cornerstone of affordable housing projects. The reduced construction time, lower labor costs, and minimized environmental footprint position precast housing as a forward-thinking solution for communities focused on sustainability and efficiency. For those considering more durable and cost-effective housing, pre-engineered buildings offer a similar approach with comparable benefits.
In the following sections, we will explore the many advantages, cost savings, and sustainability benefits that make precast housing an ideal option for affordable, resilient, and eco-friendly living spaces.
Discover how precast construction enhances PEB building benefits by visiting our PEB Buildings Benefits, Features & Applications page, where we detail the numerous advantages.
Advantages of Precast Housing
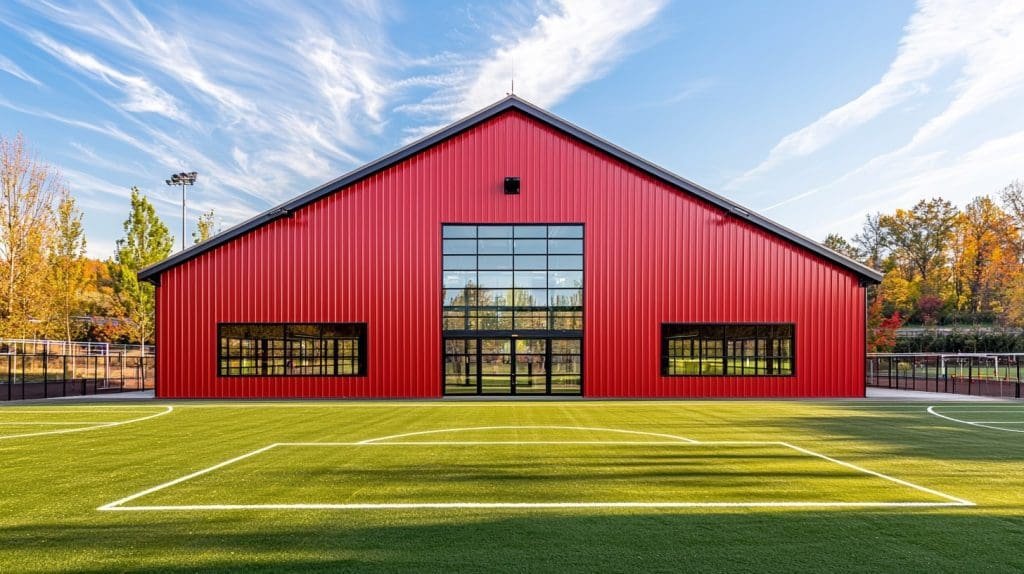
Speed of Construction
One of the most significant advantages of precast housing is the speed of construction. Because components like walls, floors, and beams are manufactured off-site in a factory, they can be produced simultaneously while the foundation is being prepared on-site. This parallel process minimizes the overall construction time. Once the precast concrete sections are complete, they are transported to the site and quickly assembled, enabling projects to be finished in weeks rather than months. For urban areas where housing demands are high, this swift setup makes modular construction and precast methods invaluable, especially for large-scale residential projects.
This faster timeline not only meets urgent housing needs but also reduces on-site labor costs and other expenses associated with prolonged construction.
Cost-Effectiveness and Consistent Quality
Precast housing offers excellent cost savings compared to traditional building methods. In conventional construction, much of the work is done on-site, requiring significant labor and time, both of which drive up costs. Precast components are manufactured in a controlled environment, which reduces waste, ensures high-quality control, and uses fewer resources overall. This efficiency allows for lower production costs, which translates into affordable housing options for end-users. By using pre-engineered buildings and other modular techniques, construction firms can also deliver consistently high-quality structures with minimal on-site variation.
The controlled environment in which precast concrete is produced leads to durable, uniform components, reducing the likelihood of costly repairs down the road.
Labor and Resource Efficiency
In areas where labor is costly or skilled workers are limited, precast housing is a smart alternative. Since much of the work is done off-site, fewer on-site laborers are needed, minimizing labor costs. The streamlined process in a factory setting also conserves materials, allowing manufacturers to reduce waste by recycling and reusing leftover concrete or materials. This approach aligns with the resource-efficient practices seen in container houses and portable cabins, where the controlled environment helps to reduce excess material and maximize productivity.
This efficiency means that projects are not only affordable but also less wasteful, contributing to the environmental benefits of choosing precast construction.
Improved Safety and Working Conditions
Precast housing construction offers improved safety conditions for workers. Because much of the assembly happens in a factory, the risks associated with on-site construction—such as falls, heavy equipment injuries, and exposure to harsh weather—are significantly reduced. By minimizing the amount of work required on-site, precast construction promotes safer work environments, which is crucial for large residential projects or commercial spaces where worker safety is a top priority.
In addition to on-site safety, working in a factory setting allows for better monitoring and maintenance of safety standards, which contributes to the quality and reliability of the final product.
Minimal Disruption to Surrounding Areas
In densely populated urban areas or eco-sensitive zones, minimizing construction disruption is essential. Precast housing construction reduces noise, dust, and general disturbance in the building’s surroundings, as on-site work is limited to the assembly phase. This approach aligns with the minimal disruption goals of portable cabins and other prefabricated structures, making it ideal for urban residential areas and communities that value reduced impact on the environment.
In summary, precast housing combines cost-efficiency, speed, and environmental sensitivity, making it a forward-looking choice for housing projects that require both quality and affordability.
Strengthen your design and engineering skills with our Design of PEB Structure: Key Elements guide, ensuring your precast homes are built to perfection.
Understanding Precast Concrete for Housing
What is Precast Concrete and How is it Used in Housing?
Precast concrete is a construction material produced by casting concrete in a reusable mold within a controlled environment, rather than directly on the building site. Once cured, the concrete components are transported to the site and assembled to form the structure of a house. This method is especially beneficial in housing because it allows for large sections—like walls, floors, and beams—to be built simultaneously and assembled quickly. Precast housing relies on these durable, factory-made components to streamline construction and improve overall quality. Similar to modular prefab buildings, precast concrete housing offers consistent quality control and flexibility in design, meeting the demands of both urban and rural projects.
This efficient approach supports faster builds and higher-quality structures, essential in meeting modern housing demands.
Types of Precast Concrete Components in Housing
In precast housing, various types of concrete components are utilized to create durable, functional homes. These include:
- Walls: Precast walls provide a sturdy, weather-resistant structure, eliminating the need for time-consuming bricklaying.
- Floors and Slabs: Precast slabs offer a flat, uniform surface, reducing on-site work and ensuring consistent floor quality.
- Beams and Columns: These components provide structural support, allowing for open floor plans and efficient load distribution.
Each of these components is manufactured in a controlled factory setting, where conditions can be carefully monitored, ensuring high-quality output. The flexibility of precast concrete allows builders to produce components of various shapes and sizes, tailored to fit specific architectural plans. The adaptability is similar to container houses and other prefab solutions, offering modularity while maintaining robust construction.
Strength and Durability of Precast Concrete Homes
Precast concrete is known for its durability and resilience, making it ideal for housing that needs to withstand diverse weather conditions, from high winds to heavy rains. The high-density concrete used in precast components provides excellent resistance to fire, termites, and general wear and tear, which is beneficial in both urban and rural settings. This durability reduces maintenance needs over time, providing long-term cost savings for homeowners. Precast homes are comparable to pre-engineered buildings in terms of robustness, offering a lasting, reliable solution for affordable housing.
This strength and low-maintenance advantage make precast homes a preferred option for homeowners seeking quality and longevity.
Quality Control and Consistency in Precast Concrete Production
Producing concrete components in a factory setting ensures precise quality control, an essential factor in residential construction. With precast housing, each piece is manufactured in a controlled environment, where concrete mix, curing times, and temperature are managed to ensure consistency and strength. This level of quality control is often harder to achieve with on-site concrete pouring, where conditions are less predictable. By using portable cabins and precast methods, construction projects benefit from reduced errors and improved quality, as each piece meets strict specifications.
This consistency contributes to the long-term durability and performance of the home, offering a housing solution that’s both reliable and efficient.
Environmental Benefits of Using Precast Concrete
Beyond quality and durability, precast concrete offers environmental benefits by reducing waste and lowering energy consumption. The controlled production environment allows manufacturers to use only the necessary materials, cutting down on excess and enabling recycling of unused concrete. Additionally, precast concrete’s thermal properties help in regulating indoor temperatures, leading to energy savings. Like portable cabins, these sustainable attributes make precast housing a greener choice, supporting energy efficiency and reducing the environmental impact of construction.
Overall, understanding the materials and methods behind precast concrete helps in recognizing its value for modern, sustainable, and resilient housing solutions.
Ensure quality in your precast projects by partnering with top manufacturers listed on our PEB Building Manufacturers in India page, known for their excellence.
Low-Cost Housing Options with Precast Technology
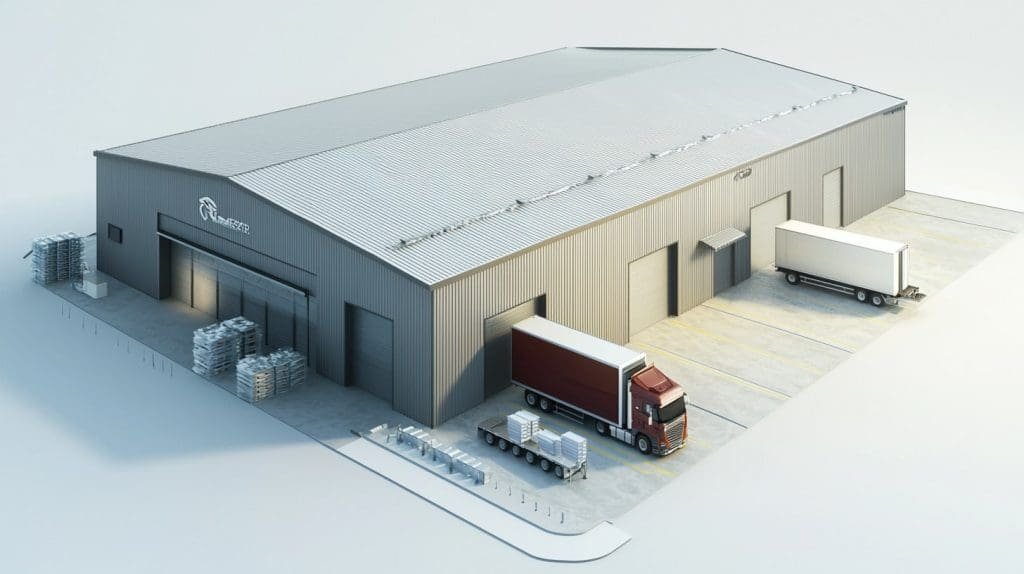
How Precast Technology Reduces Construction Costs
Precast housing is gaining traction as an affordable solution, especially for low-cost housing projects in both urban and rural areas. By manufacturing components off-site, precast construction significantly reduces on-site labor, material waste, and the time required to complete a project. This cost-saving approach translates into lower overall expenses for homeowners and developers alike. Unlike traditional construction, which often requires extensive manpower, precast technology allows for efficient, streamlined assembly, bringing down the costs of both labor and materials. Modular prefab buildings and other prefabricated structures share this advantage, offering an economical choice for residential developments.
These savings make precast technology especially valuable in housing projects aimed at affordability, meeting the needs of cost-conscious homebuyers without sacrificing quality.
Ideal Solution for Affordable Housing Initiatives
Due to its cost-effectiveness, precast technology is often the preferred choice in affordable housing initiatives. By enabling faster construction and ensuring consistent quality, precast housing can help meet the growing demand for affordable homes in India and globally. Governments and private developers are increasingly adopting precast methods for large-scale housing projects, as they allow for rapid construction at a fraction of traditional costs. Precast components, like walls and slabs, can be mass-produced, making it easier to deliver large housing units in a short time frame, similar to the efficiency seen in container houses for modular living solutions.
By leveraging precast construction, developers can address housing shortages, particularly in regions where affordable housing is urgently needed.
Examples of Successful Low-Cost Precast Housing Projects
Across the globe, successful low-cost housing projects have demonstrated the effectiveness of precast technology. Countries like China, Brazil, and South Africa have utilized precast methods to deliver homes quickly and affordably, achieving impressive results for large residential communities. In India, precast technology is increasingly used in metropolitan areas for budget-friendly housing that meets local quality standards. This approach to housing mirrors the benefits seen in pre-engineered buildings, which also offer economical and time-efficient building solutions.
These examples showcase how precast technology is transforming housing projects by delivering quality homes at lower costs, particularly in densely populated areas.
Energy and Cost Savings Through Thermal Efficiency
Precast concrete’s thermal efficiency also contributes to cost savings in the long run. The dense structure of precast concrete provides excellent insulation, helping to maintain a stable indoor temperature and reducing the need for heating and cooling. This energy efficiency is especially valuable in low-cost housing, where utility savings over time are a priority for homeowners. Many portable cabins and other prefabricated structures incorporate similar energy-saving features, making them economical for residential and commercial use alike.
By reducing energy consumption, precast housing not only lowers costs for residents but also promotes a sustainable lifestyle, aligning with global goals for energy-efficient living.
Accessibility of Precast Homes in Both Urban and Rural Areas
The adaptability and affordability of precast homes make them suitable for both urban and rural locations. In urban settings, they offer a quick solution for affordable apartment complexes and community housing projects. In rural areas, where transportation of materials can be challenging, precast homes allow for efficient and accessible construction that meets local needs. The ease of setup and lower transportation costs also make portable cabins a practical choice, providing housing solutions that are adaptable to various environments.
Ultimately, the affordability and efficiency of precast technology make it a game-changer in the housing industry, addressing the pressing need for low-cost, high-quality housing solutions in a way that’s accessible to all.
Broaden your prefab housing expertise by exploring our Prefabricated Houses in Hyderabad projects, showcasing effective implementations.
Durability and Longevity of Precast Homes
Built to Last: Strength of Precast Concrete
One of the standout qualities of precast homes is their exceptional durability. Precast concrete is renowned for its strength and resilience, making it ideal for constructing homes that can withstand various environmental and physical stresses. The dense, reinforced structure of precast concrete panels offers excellent resistance to cracking, moisture, and natural wear, which is essential for long-term durability. This level of sturdiness parallels the reliability seen in modular prefab buildings, which are also designed to provide secure, lasting solutions.
Because of this resilience, precast homes require minimal maintenance over the years, providing homeowners with peace of mind and reducing the likelihood of costly repairs.
Resistance to Natural Elements and Environmental Factors
Precast homes are constructed to resist a variety of natural elements, including extreme weather conditions such as heavy rains, high winds, and intense sunlight. The dense, non-porous nature of precast concrete makes it water-resistant, which prevents mold and mildew buildup that can occur in more porous building materials. Additionally, precast concrete is highly fire-resistant, providing an added layer of safety that is particularly valuable in areas prone to fires. Much like container houses and other prefabricated options, precast homes are built to perform under challenging environmental conditions, ensuring both longevity and safety.
This resistance to environmental factors makes precast homes suitable for various climates, from tropical regions to areas with more temperate conditions.
Low Maintenance Requirements
One of the long-term benefits of precast housing is its low maintenance. Unlike traditional brick or wood homes, which often require periodic repairs due to environmental wear, precast homes are made with materials that are inherently durable and require minimal upkeep. Homeowners won’t have to worry about issues like termite infestations, warping, or erosion, as the concrete panels are highly resistant to these common maintenance challenges. For example, portable cabins and other prefabricated constructions often include similar low-maintenance materials, reducing the need for constant care and attention.
This durability allows homeowners to enjoy their living space without the burden of frequent repairs, lowering long-term ownership costs.
Extended Lifespan and Investment Value
Precast concrete homes are designed with a lifespan that can outlast many conventional building materials. Due to their resilience, they provide lasting value, making them a smart investment for buyers seeking a home that can serve multiple generations. The robustness of precast concrete allows these homes to maintain structural integrity over decades, adding to their investment appeal. Much like pre-engineered buildings, which offer strong, reliable structures, precast homes ensure that owners gain long-term value from their investment.
For those looking to invest in real estate, the longevity of precast homes provides assurance that the property will retain its value over time, adding stability to any housing market.
Eco-Friendly Advantages Due to Durability
The durability of precast homes also offers environmental benefits by reducing the need for frequent renovations or rebuilds. This extended lifespan minimizes the consumption of additional resources, such as materials and energy, that would otherwise be required for ongoing maintenance or repairs. The eco-friendliness of low-maintenance housing options like portable cabins and other prefab solutions also supports sustainability, aligning with modern priorities for environmentally responsible construction.
In summary, the long-lasting nature of precast homes makes them a reliable, low-maintenance option that meets the needs of both homeowners and the environment, reinforcing their role as a durable, sustainable housing solution.
Discover a variety of prefab solutions by visiting our Prefabricated Houses in Kerala guide, highlighting successful projects in Kerala.
Environmental Benefits of Precast Housing
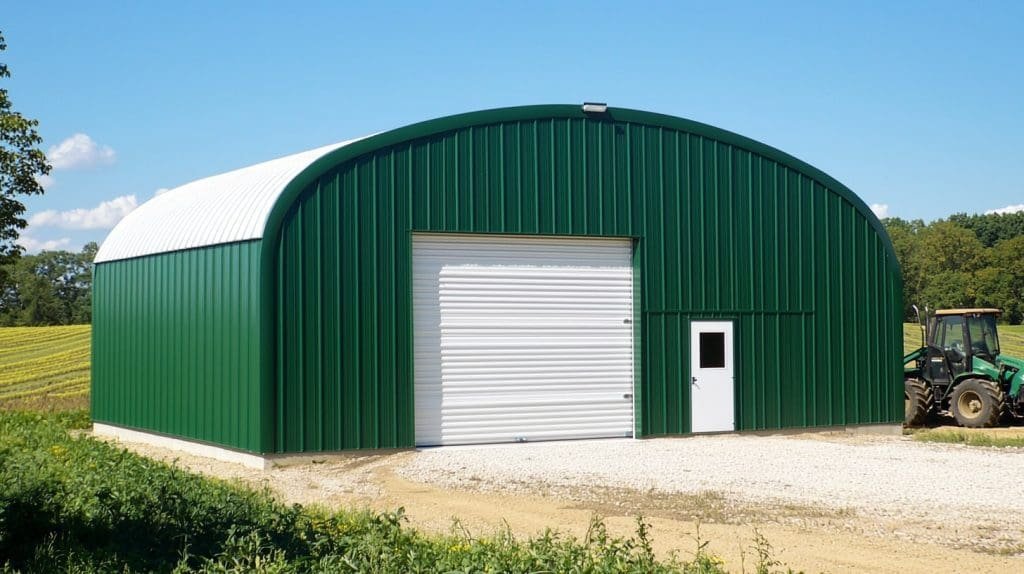
Eco-Friendly Construction Process
Precast housing is an environmentally responsible choice due to its efficient construction process, which generates less waste and requires fewer resources than traditional building methods. Manufacturing precast concrete components in a controlled factory environment allows for precise material usage, minimizing excess and promoting recycling of unused materials. This approach is similar to the sustainable practices seen in modular prefab buildings, which are also designed to optimize resources and reduce construction waste.
With lower material waste and reduced on-site construction time, precast housing contributes to a cleaner building process that aligns with sustainability goals and reduces the overall carbon footprint of residential projects.
Reduced Energy Consumption and Emissions
The controlled factory setting used in precast construction not only improves quality but also reduces energy consumption. In traditional construction, on-site processes consume a considerable amount of energy due to extended timelines, machinery use, and continuous material transportation. Precast housing eliminates much of this by consolidating production in one location, reducing the need for on-site work and associated energy usage. Many container houses and other prefab options share this energy-efficient approach, making them ideal for projects that prioritize reduced emissions and energy conservation.
Lower energy requirements during construction contribute to a more sustainable housing solution that benefits both homeowners and the environment.
Use of Recycled and Sustainable Materials
Precast housing often incorporates recycled materials, including recycled concrete and steel, which further enhances its environmental benefits. By using sustainable resources, manufacturers can lower the demand for new raw materials, thus reducing environmental impact. Recycled materials used in the production of precast components help conserve natural resources and contribute to a circular economy. This commitment to sustainability is also seen in portable cabins, which frequently use recyclable materials and eco-friendly practices to support green building initiatives.
For homeowners and developers focused on eco-conscious construction, the use of recycled materials in precast housing provides an effective way to support environmental responsibility.
Energy Efficiency in Everyday Use
In addition to being eco-friendly during construction, precast homes also offer energy efficiency for residents. The dense structure of precast concrete provides excellent insulation, which helps regulate indoor temperatures by keeping interiors cool in the summer and warm in the winter. This thermal efficiency reduces the need for air conditioning and heating, leading to lower energy consumption and cost savings over time. Similarly, portable modular units often incorporate insulated panels to enhance energy savings, aligning with the sustainability goals of modern housing.
For homeowners, these energy-efficient benefits mean reduced utility bills and a smaller environmental footprint, adding to the appeal of precast housing as a sustainable option.
Minimal Environmental Disruption During Installation
The installation of precast housing components requires less on-site work, reducing disruption to the surrounding environment. Traditional construction often impacts local ecosystems due to extensive groundwork, noise, and pollution. By contrast, precast homes can be assembled quickly, minimizing the time and resources needed on-site and reducing the environmental impact. This is particularly beneficial for residential areas or eco-sensitive zones, where preserving the natural environment is a priority. Much like portable cabins, precast homes are designed to integrate with the landscape with minimal intrusion.
In conclusion, the environmental benefits of precast housing make it an attractive choice for those looking to adopt sustainable, eco-friendly practices in their housing projects, providing an option that supports a greener future.
Gain insights from our Prefabricated House in Pune Overview page, which showcases successful prefab projects in Pune.
Speed and Efficiency in Precast Housing Construction
Accelerated Construction Timelines
Precast housing is known for its rapid construction timeline, offering an efficient alternative to traditional on-site building methods. Because the concrete components are manufactured in a controlled factory environment, multiple pieces can be produced simultaneously and stored until they are ready for transport. While the site is being prepared, these components are completed and cured, allowing for faster assembly once on-site. This parallel process significantly reduces the total construction time compared to conventional construction methods. Similar to modular prefab buildings, precast housing provides a streamlined process that meets tight project deadlines and ensures timely completion.
This efficiency is invaluable in projects with high demand, such as urban housing developments, where speed is critical to meet the needs of growing populations.
Reduced On-Site Labor and Resource Use
One of the benefits of precast housing is the reduction in on-site labor, which not only lowers costs but also simplifies project management. Since most of the work is done off-site, there is less need for large teams of laborers at the construction site. This reduction in on-site activity decreases the likelihood of delays due to labor shortages or adverse weather conditions. Precast components, once delivered, are quickly assembled, much like container houses, which arrive mostly finished and require minimal additional work on-site.
This reduction in labor and resource use not only saves money but also enhances the efficiency and predictability of the construction timeline, making it ideal for projects with strict deadlines.
Minimal Weather Delays and Year-Round Construction
Traditional construction is often hampered by weather-related delays, which can extend project timelines and increase costs. Precast housing, however, mitigates this issue since most of the construction work is completed indoors within a factory setting. Regardless of external weather conditions, precast components are produced in a stable environment, ensuring consistent progress on the project. Once the pieces are ready, the on-site assembly is relatively fast and less dependent on weather, much like portable cabins, which are designed to be transported and set up quickly.
This flexibility allows precast housing projects to continue year-round, even in locations with challenging weather, contributing to reliable project timelines.
Enhanced Quality Control and Precision
The factory setting used in precast construction allows for stringent quality control, ensuring that each component meets precise specifications. Since the production environment is tightly controlled, manufacturers can monitor every aspect of the process, from concrete mix to curing conditions, resulting in components that are uniform and reliable. This level of precision reduces on-site adjustments and rework, improving the overall efficiency of the construction process. Much like pre-engineered buildings, which benefit from controlled production, precast housing offers a high-quality final product with fewer on-site issues.
Enhanced quality control contributes to the durability and safety of the structure, giving homeowners confidence in the long-term reliability of their investment.
Optimized Logistics and Transport
The efficiency of precast housing extends to logistics as well. Precast components are manufactured, stored, and transported according to a carefully coordinated schedule, ensuring that each piece arrives on-site exactly when needed. This optimized logistics approach minimizes delays, reduces storage needs on-site, and prevents overcrowding. This logistical efficiency is similar to the planning required for portable modular units, where transport and setup are handled with precision to ensure smooth installation.
In summary, the speed and efficiency of precast housing construction make it an ideal choice for projects that require fast, cost-effective, and high-quality solutions, meeting the needs of both developers and homeowners alike.
Optimize your agricultural housing with guidance from our Prefab Farm Homes India Guide, tailored to meet farm living needs.
Structural Benefits and Safety of Precast Concrete Homes
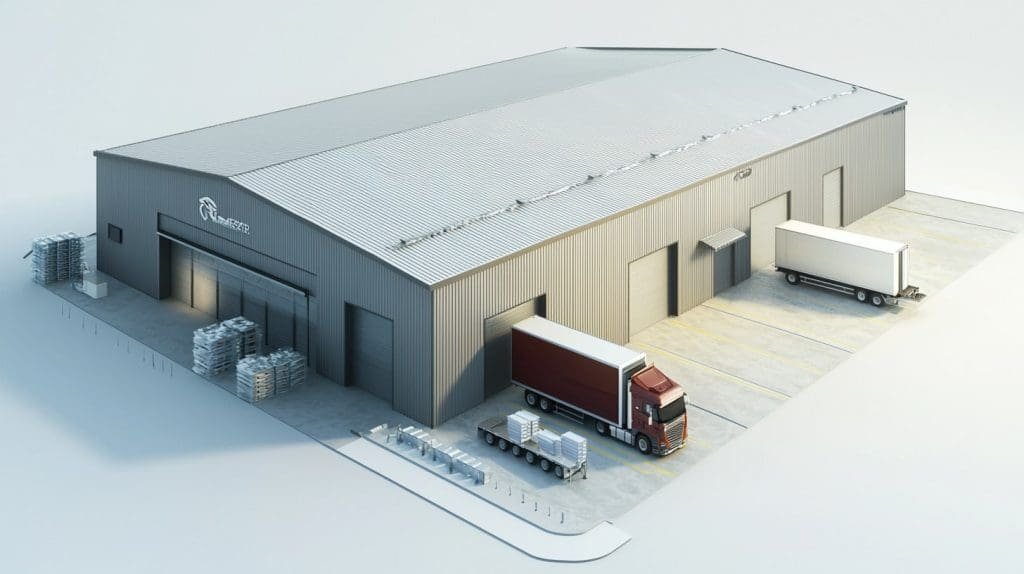
High Structural Integrity for Enhanced Safety
Precast concrete homes are known for their high structural integrity, making them one of the safest and most durable housing options available. Manufactured in a controlled factory setting, precast components are made with reinforced concrete, ensuring they are sturdy and able to handle various environmental stresses. This robust structure provides enhanced protection against natural forces, from strong winds to seismic activity, making precast homes an ideal choice for regions with extreme weather conditions. Much like modular prefab buildings, which are designed for resilience, precast homes offer an extra layer of safety for residents.
The reinforced structure of precast homes minimizes the risk of structural failures, providing long-lasting stability and safety for occupants.
Fire Resistance and Safety Standards
One of the critical safety advantages of precast concrete is its excellent fire resistance. Unlike wood or other traditional building materials, concrete is non-combustible, which means that it won’t catch fire or contribute to the spread of flames. Precast concrete homes can endure high temperatures without compromising their structural integrity, providing occupants with vital protection in case of a fire. This makes them comparable to container houses, which also offer solid fire resistance due to their metal construction.
This fire resistance not only enhances the safety of precast homes but also often results in lower insurance premiums, adding a financial benefit for homeowners.
Earthquake Resistance and Stability
In earthquake-prone areas, the flexibility and resilience of precast concrete can make a significant difference. Precast components are reinforced and designed to handle seismic forces, making them less likely to crack or break under pressure. The interconnected nature of precast walls, beams, and floors provides stability and distributes stress evenly across the structure, helping the building withstand ground movement. Portable cabins and other prefabricated structures with reinforced frameworks share this advantage, as they are built to remain stable in dynamic conditions.
The earthquake resistance of precast homes adds a vital layer of security, particularly in regions with high seismic activity, ensuring that structures remain safe and sound.
Pest and Mold Resistance for Healthier Living
Precast concrete’s non-porous surface and moisture resistance provide natural protection against pests and mold. Traditional homes made of wood or drywall are often susceptible to termite infestations and mold growth, especially in humid environments. However, precast concrete does not attract pests, and its water resistance helps prevent mold and mildew buildup, creating a healthier living environment. Similar to pre-engineered buildings that utilize durable materials, precast homes offer low maintenance and a safer environment for residents.
This resistance to pests and mold not only extends the life of the building but also contributes to better indoor air quality and a healthier home.
Sound Insulation for Added Comfort and Privacy
Precast concrete homes offer excellent sound insulation, making them ideal for areas where noise reduction is a priority. The dense structure of concrete naturally dampens sound, minimizing the transmission of noise between rooms and from outside sources. This added privacy is particularly beneficial for homes in busy urban areas or multi-family buildings where sound control is important. The soundproofing benefits of precast concrete are similar to those seen in portable modular units, which are also built with materials that enhance sound insulation.
With soundproofing, pest resistance, fire and earthquake resilience, precast homes provide a secure and comfortable living environment, supporting the modern demand for safe, high-quality housing.
Tackle urban construction challenges with our Prefab Homes Mumbai Guide, offering strategies designed for Mumbai’s dynamic environment.
Customization Options for Precast Homes
Versatile Layouts to Fit Diverse Needs
One of the greatest benefits of precast homes is their flexibility in layout and design, which allows homeowners to personalize their living spaces to suit specific needs and preferences. Precast homes can be built with a variety of layouts, including open floor plans, multi-room configurations, and custom features like extended balconies or spacious patios. This adaptability makes precast housing ideal for individuals or families who desire a home tailored to their lifestyle. Much like modular prefab buildings, precast homes offer modular options, making it easy to add or rearrange rooms based on the needs of the household.
This flexibility ensures that homeowners get a home that aligns perfectly with their vision, providing both functionality and aesthetic appeal.
Interior and Exterior Finishes for Personal Style
Precast homes come with a wide range of customizable finishes, allowing owners to create interiors and exteriors that reflect their personal style. For the exterior, options like stone veneers, textured surfaces, or smooth finishes can help the home blend with the surrounding environment or stand out as a unique structure. Inside, homeowners can choose various wall textures, flooring materials, and paint colors to create a comfortable and personalized living space. Many container houses also offer customization in finishes, giving residents control over the look and feel of their homes.
These customizable finishes add personality and charm to precast homes, transforming them into spaces that feel unique and inviting.
Eco-Friendly Features and Sustainable Design Choices
For those who prioritize sustainability, precast homes offer a range of eco-friendly options. Homeowners can choose energy-efficient windows, solar panels, and insulated walls to make their homes more sustainable and reduce energy costs. Rainwater harvesting systems and low-flow water fixtures can be added to support water conservation efforts, which is particularly beneficial in areas prone to water scarcity. Portable cabins often include similar eco-conscious features, making them a smart choice for environmentally aware buyers.
These sustainable choices not only contribute to a greener lifestyle but also add long-term savings on utilities, making precast homes both economical and eco-friendly.
Smart Home Integration for Modern Living
Modern precast homes can be outfitted with the latest smart home technology to enhance convenience and security. Home automation systems for lighting, climate control, and security can be seamlessly integrated into the home’s design, providing homeowners with control over their living environment from their smartphones or other devices. Precast homes, much like pre-engineered buildings, are easily adaptable to technology, allowing for a smooth integration of smart features.
These smart home options enable homeowners to manage energy use more efficiently and enhance security, adding another layer of comfort and modernity to precast homes.
Adaptable Spaces for Multi-Functional Living
In addition to basic customization, precast homes can be designed to serve multiple functions, making them suitable for diverse living requirements. From additional storage areas to home offices and guest rooms, the modular nature of precast housing allows for versatile spaces that can be repurposed as needed. Similar to portable modular units, which are used in various settings, precast homes offer adaptable designs that cater to the changing needs of homeowners.
In summary, the customization options for precast homes make them an attractive choice for homeowners seeking style, functionality, and flexibility. By allowing for tailored layouts, finishes, sustainable features, and smart home technology, precast homes provide a personalized living experience that meets the diverse demands of modern lifestyles.
For an extensive understanding of precast and prefab housing benefits, revisit our PEB Buildings Benefits, Features & Applications page. It’s your ultimate resource for PEB information.
Future of Precast Housing and Construction in India
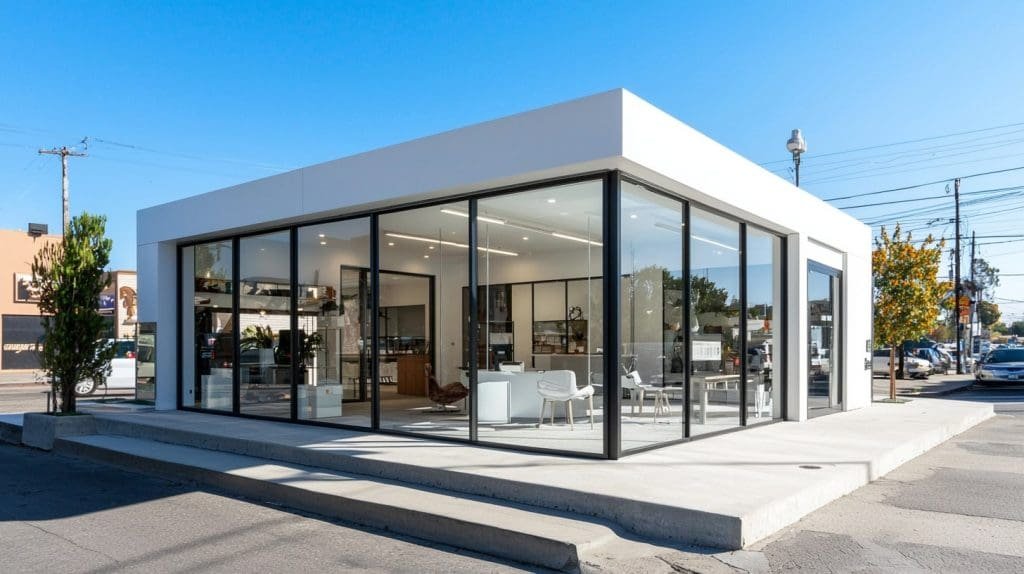
Growing Demand Due to Rapid Urbanization
As India continues to experience rapid urbanization, the demand for affordable, efficient, and high-quality housing is increasing significantly. Precast housing meets these demands by providing quick, cost-effective solutions that can be easily scaled to accommodate large residential developments. Urban areas with limited space and high population density benefit from precast construction, which allows for multi-story apartment buildings and modular housing units that maximize land use. This demand reflects a similar interest in modular prefab buildings, which also offer efficient, space-saving solutions suited to urban environments.
By embracing precast housing, cities in India can address the growing housing needs of their populations with structures that are both durable and adaptable.
Innovative Technology Driving Precast Advancements
The precast housing sector in India is evolving as new technologies continue to enhance the efficiency and quality of construction. Innovations like 3D printing, Building Information Modeling (BIM), and automated production lines are being integrated into the precast industry, allowing for more precise and complex designs. These technologies enable manufacturers to create custom precast components with a high degree of accuracy, reducing material waste and ensuring a consistent standard of quality. Similar to advancements seen in container houses, which utilize modular designs and modern materials, these innovations push precast housing forward, making it a viable option for future urban and rural developments.
With these technological advancements, India’s precast industry is better positioned to meet the demands of a rapidly modernizing housing market.
Government Support and Policy Initiatives
Government initiatives in India are also fostering the growth of the precast housing sector. Policies promoting affordable housing, sustainable construction practices, and infrastructure development align with the benefits of precast construction. Programs like the Pradhan Mantri Awas Yojana (PMAY), which aims to provide affordable housing to all, encourage the adoption of innovative and cost-effective building techniques, including precast. Similar support is given to portable cabins and other prefabricated structures that contribute to the country’s infrastructure needs, making government backing a significant driver for the industry.
This governmental focus on affordable housing and sustainable practices makes precast housing an essential part of India’s housing and infrastructure landscape.
Environmental Considerations and Sustainable Development
As the importance of sustainability grows, the precast housing industry is expected to play a key role in India’s shift toward environmentally responsible construction. Precast concrete’s low waste production, minimal energy usage, and reduced on-site disturbance align well with green building principles. Additionally, the energy efficiency of precast homes—achieved through high thermal insulation and reduced reliance on heating or cooling systems—supports a lower carbon footprint, which is increasingly valued in both urban and rural areas. Similar to portable modular units, which are often designed with sustainability in mind, precast housing appeals to eco-conscious buyers.
As environmental concerns continue to shape the construction industry, precast housing offers a forward-looking solution for sustainable urban and rural developments.
Adapting to Rural and Urban Housing Needs
The adaptability of precast housing makes it a versatile choice for both rural and urban settings in India. In rural areas, precast homes offer affordable, durable, and low-maintenance options that can withstand harsh weather conditions, while in cities, they provide high-density housing solutions. Precast construction also allows for design flexibility, meeting the needs of different communities and supporting diverse architectural styles. This adaptability is shared by pre-engineered buildings, which are used in various settings due to their customizable designs and reliable structure.
The future of precast housing in India is bright, as it combines efficiency, affordability, and sustainability—qualities that align perfectly with the needs of a growing, environmentally conscious population.
Precast housing represents a revolutionary approach to modern construction, offering efficient, durable, and eco-friendly solutions that address the diverse housing needs across India. From rapid urbanization to sustainable development, precast homes provide a versatile and cost-effective alternative to traditional construction, making them ideal for urban high-rises and rural settings alike. With strong government support, technological advancements, and growing awareness of sustainable building practices, precast housing is set to play an essential role in India’s future housing and infrastructure landscape.
For those interested in exploring high-quality, customizable precast options, our company is committed to delivering solutions that combine durability, flexibility, and affordability. To learn more about our values, vision, and products, please visit our About Us page for additional insights into our dedication to sustainable and efficient building solutions across India.
FAQs about Precast Housing and Construction
1. What is precast housing, and how does it differ from traditional construction?
Precast housing involves manufacturing concrete components in a factory and assembling them on-site, whereas traditional construction builds everything on-site. This method speeds up construction and ensures consistent quality.
2. Are precast homes durable enough for Indian climates?
Yes, precast homes are highly durable and can withstand a range of environmental factors, including heavy rains, high winds, and extreme heat, making them well-suited for India’s varied climates.
3. How affordable is precast housing compared to conventional homes?
Precast homes are generally more cost-effective due to reduced labor and faster construction times, making them an ideal choice for affordable housing projects.
4. Can precast homes be customized in terms of layout and design?
Yes, precast homes offer a wide range of customization options, including layout configurations, interior finishes, and eco-friendly features, allowing homeowners to tailor the home to their needs.
5. What materials are used in precast housing construction?
Precast housing primarily uses reinforced concrete, which is manufactured to be strong, durable, and resistant to pests, moisture, and fire, making it ideal for long-lasting homes.
6. How eco-friendly is precast housing?
Precast housing is environmentally friendly due to its reduced waste, energy efficiency, and the ability to incorporate recycled materials. It also provides thermal insulation, reducing energy consumption for heating and cooling.
7. How long does it take to build a precast home?
Precast homes can be completed much faster than traditional homes. While the factory produces components, the foundation is prepared on-site, and assembly typically takes a few weeks.
8. Do precast homes require regular maintenance?
Precast homes require minimal maintenance due to the durability of concrete, which resists mold, pests, and environmental wear, making them low-maintenance and cost-effective.
9. Are precast homes safe in areas with earthquakes or fires?
Yes, precast homes are structurally sound and designed to resist seismic forces. Additionally, concrete is non-combustible, offering high resistance to fire, making these homes safer.
10. Is precast housing suitable for both urban and rural areas?
Absolutely. Precast housing’s adaptability allows it to fit well in both urban and rural settings, providing high-density housing in cities and durable, affordable solutions in rural regions.
The post was very good, I appreciate how you explain it, Keep the posts coming! Very good talent.”