PEB Shed Cost: Affordable, Durable, and Customizable Solutions for Industrial Needs
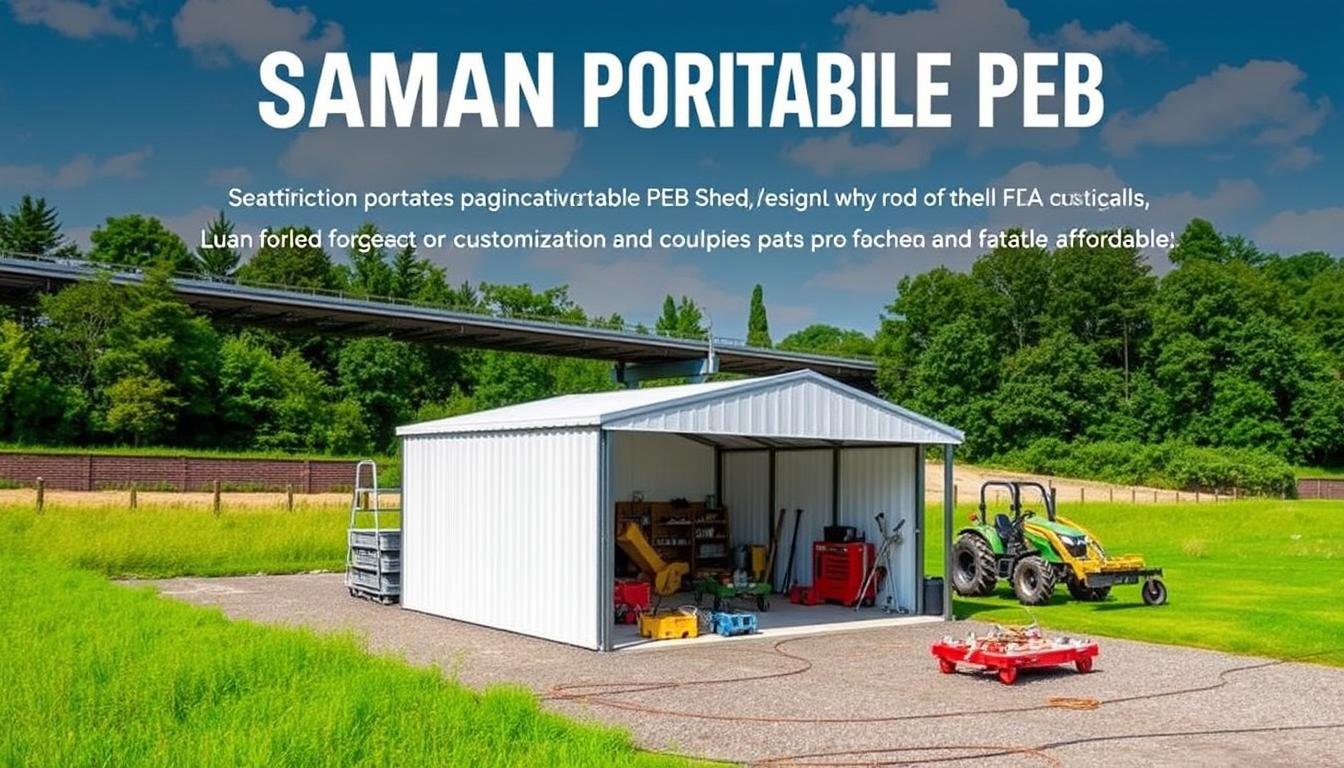
Are you fed up with high construction costs and long wait times? Imagine a solution that changes your industrial space without breaking the bank.
Pre-Engineered Building (PEB) sheds are changing the game in India. They cost between ₹100 to ₹400 per square foot. These structures are affordable, strong, and can be tailored to fit your needs.
The construction scene in India is shifting fast. More than 80% of industrial projects use PEB technology. This cuts construction time by up to 50% compared to old methods. Our guide will dive into PEB structures, showing how they save money and last long.
Key Takeaways
- PEB shed costs are significantly lower than traditional construction methods
- Customizable solutions available for various industrial applications
- Rapid installation reduces project timelines
- High durability with resistance to environmental factors
- Energy-efficient and sustainable building solution
- Flexible design options to meet specific project requirements
Understanding Pre-Engineered Building Solutions
Pre-engineered buildings (PEBs) are changing the game in industrial construction. They offer new ways to build that are faster and more efficient. Our analysis shows how PEBs are making a big impact in India.
PEB systems are built with great care, bringing big advantages to warehouses and industrial sites. Their unique design and making process save money and time.
Core Components of PEB Systems
The main parts of PEB systems are:
- Primary steel frames
- Secondary structural elements
- Roof and wall panels
- Foundation systems
- Customizable architectural elements
These parts work together to make strong yet light buildings. PEB buildings are up to 30% lighter than regular steel buildings. This means less material and money saved on transport.
Steel like E250 and E350 is often used, costing between ₹90/kg and ₹400/sq ft. PEBs are made to fit together well, making the most of space and using less material.
PEB solutions use the latest in making things, giving great value. They are made off-site, reducing waste and speeding up building. This saves a lot of money in the long run for industrial projects.
PEB Shed Cost: Breaking Down the Investment
PEB sheds offer big savings for industrial projects. They cost less than traditional buildings. This makes them a smart choice for businesses.
What makes PEB sheds affordable includes:
- Material optimization
- Lightweight structural components
- Prefabrication efficiency
- Reduced on-site labor requirements
Our study shows PEB sheds save a lot of money. Prefabricated industrial structures can cut initial costs by 30-40%. They are made in a factory, which means less waste and lower costs.
Important things to think about for PEB sheds are:
- Faster construction timelines
- Lower labor expenses
- Minimal on-site fabrication
- Reduced transportation and handling costs
Companies that choose PEB sheds save money in the long run. These buildings are light, which means less foundation work and cheaper to move. With the right design and a good manufacturer, businesses can save money and get a strong building.
Cost Comparison with Traditional Construction Methods
Businesses looking for affordable portable cabins are turning to pre-engineered building (PEB) solutions. These new construction methods offer big savings over traditional ways.
The construction world is changing fast, with PEB systems leading the way for modern businesses. Our study shows big cost savings:
- Labor cost reduction of 30-50% compared to conventional construction
- Construction timeline compressed by 50-75%
- Material efficiency leading to 10-20% cost savings
Labor Cost Reduction Benefits
Durable container office designs save a lot on labor. Traditional building needs a lot of on-site workers. But PEB solutions make building faster and cheaper.
The average labor cost in traditional construction is $25 to $75 per hour. PEB is a great choice for businesses watching their budget.
Material Efficiency Savings
PEB construction is great at saving materials. It uses offsite fabrication and precise manufacturing to cut down waste. Controlled manufacturing environments ensure optimal material usage, saving businesses money.
Timeline-Related Cost Benefits
PEB solutions are fast, which saves money. Projects finish 30-50% faster than traditional methods. This means businesses can start making money sooner and save on project costs.
Choosing PEB solutions can help businesses see a return on investment in 5-7 years. This is much faster than traditional construction.
Material Selection and Cost Implications
Choosing the right materials is key for making top-notch porta cabins and worker colonies. Pre-engineered buildings use the latest materials to save money and work better.
Steel is the main material in PEBs, and it has big benefits:
- High-tensile steel gives great strength without being too heavy
- Light frames cut down on the weight of the building
- Cold-rolled parts make the structure last longer
- Insulated panels help save energy
The choice of materials affects the upfront cost and ongoing expenses. Prefabrication technologies help cut down on waste and make building faster.
Different types of sheets offer many design options:
- Metal roofing sheets keep the weather out
- Corrugated sheets add strength
- Insulated wall panels control temperature
- Façade panels improve looks and function
By looking at material features, we can find affordable ways to meet industrial and worker needs. This way, we keep quality and efficiency high.
Design Customization and Pricing Factors
Pre-engineered buildings (PEBs) offer great flexibility in design. They let businesses create solutions that fit their needs. Whether it’s a unique container cafe or an industrial storage facility, the cost varies based on customization.
Customizing the design is key to the project budget. Businesses can save money by knowing what affects PEB shed costs.
Structural Configurations and Cost Implications
The design’s complexity affects the cost of a PEB shed. Different designs have their own benefits:
- Single-story designs: Most cost-effective option
- Multi-level structures: Higher complexity, increased pricing
- Specialized layouts: Custom requirements may raise expenses
Size and Dimension Pricing Dynamics
The size of a PEB shed affects the cost. In India, prices range from ₹200 to ₹400 per square foot. Bigger spaces might be cheaper overall.
Additional Features and Cost Considerations
Adding special features can improve functionality but increase costs. Some common extras include:
- Mezzanine levels
- Advanced insulation systems
- Climate control mechanisms
- Specialized interior configurations
Choosing the right features is important for staying within budget. PEB sheds are modular, making them adaptable for many uses. This includes industrial warehouses and unique spaces like container cafes.
Regional Price Variations in India
The pre-engineered building (PEB) market in India shows interesting price changes across regions. These changes affect the cost of building PEB structures. Different areas have their own pricing patterns, influenced by several key factors.
Important factors that affect PEB structure prices include:
- Local material availability
- Transportation infrastructure
- Regional labor rates
- Specific building code requirements
In big cities like Mumbai and Delhi, the cost of PEB structures is higher. Urban areas face more complex logistical issues, leading to higher construction costs.
Prices can vary by 10% to 25% in different Indian states. Southern states like Tamil Nadu and Karnataka have lower prices due to strong manufacturing bases. In contrast, the northeastern regions might have slightly higher costs because of tough terrain and limited infrastructure.
Companies planning PEB projects need to study local markets and economic conditions. This helps them manage their construction budgets better.
Construction Timeline and Cost Efficiency
Pre-engineered building (PEB) solutions change the game in industrial construction. They cut down project timelines and lower the cost of peb warehouses. Our new way of building is faster and more efficient than old methods.
Companies wanting to build fast can use PEB technology. It makes construction much quicker than traditional ways. PEB shed designs can cut construction time by 40% to 60%.
Project Planning Phases
For PEB to work well, good planning is key. The main steps are:
- Comprehensive design analysis
- Precise component fabrication
- Streamlined site preparation
- Efficient component transportation
- Rapid on-site assembly
Installation Process Overview
The PEB installation is very efficient. It’s cheaper than traditional building, so businesses save money. They can expect:
- Prefabricated components ready to assemble
- Less need for on-site labor
- Less disruption during construction
- Projects finish faster
In Chennai, a PEB shed design cut construction time from 10 months to 4 months. This shows how powerful this method can be.
Maintenance and Long-term Cost Benefits
Pre-engineered buildings (PEB) are a wise choice for businesses looking for affordable and cost-effective solutions. They offer long-term financial benefits, making them appealing to forward-thinking companies.
Our study shows several important maintenance and economic advantages:
- Lower yearly maintenance costs compared to traditional buildings
- Less wear and tear thanks to high-quality manufacturing
- Long-lasting with minimal repair needs
- Energy-efficient design cuts down on operational costs
PEB sheds are built to last. Advanced materials and manufacturing ensure they can handle tough weather while staying strong. This means businesses spend less on upkeep over time.
Financial benefits include:
- Using materials wisely cuts down initial construction costs
- Modular design makes it easy to make changes later
- Smart insulation saves on energy
- Recyclable materials help businesses go green
With over 7,400 projects and 24+ years of experience, our PEB solutions are reliable and cost-effective for industrial needs.
Environmental Benefits and Sustainability Features
We’re dedicated to building in a way that’s good for the planet. Pre-engineered building (PEB) sheds are a big step towards green industrial spaces. They offer huge benefits for companies that care about the environment.
PEB solutions stand out for their green credentials. They use smart design and materials that are better for the planet. This makes them different from old-school building methods.
Energy Efficiency Aspects
Our PEB sheds are built to save energy. They can cut energy use by 20-30% thanks to special features:
- Advanced thermal insulation systems
- Strategic natural lighting integration
- Optimized ventilation mechanisms
- Reflective roof technologies
Recyclable Materials Usage
Our porta cabin options focus on using materials that are good for the planet. PEB solutions use new ways to recycle materials:
- Up to 80% of construction materials can be reused or recycled
- Steel components are 100% recyclable
- Modular design allows for easy disassembly and repurposing
- Minimal waste generation during fabrication
By following circular economy principles, we cut down on waste. Our PEB sheds are more than just buildings. They’re a promise of sustainable growth.
Industry-Specific Applications and Pricing
Pre-engineered buildings (PEBs) have changed the game in many industries in India. They offer custom solutions for different business needs. This includes everything from worker colonies to unique container cafes for restaurants.
Our detailed study shows how PEBs fit into many industries:
- Manufacturing facilities
- Warehousing and logistics
- Cold storage units
- Sports complexes
- Agricultural storage
The cost of PEB sheds varies a lot, depending on what you need. Industrial sheds can cost between ₹100 to ₹450 per square foot. Specialized structures like waterproof godown sheds can cost up to ₹350 per square foot.
When thinking about cost, consider these factors:
- How complex the structure is
- The quality of materials used
- The size and shape of the building
- Any extra features you want
PEB technology is great for building efficient worker colonies. These buildings are built fast and are affordable. They provide good living spaces for workers in industrial areas.
Also, PEBs can turn into unique container cafes for restaurants. They offer a quick, modular, and stylish way to start new businesses.
PEB structures are priced from ₹85 per kg to ₹900 per square foot. They offer flexible solutions for businesses of all sizes. This ensures the best value and performance in various industrial uses.
Financing Options and ROI Analysis
Investing in pre-engineered buildings (PEB) is smart for businesses. The cost of a PEB shed is appealing when you look at the long-term benefits. It offers a great return on investment (ROI).
There are many ways to finance PEB projects. These methods can make your project more cost-effective:
- Traditional bank loans with competitive interest rates
- Leasing arrangements for flexible capital management
- Government incentives for sustainable construction
- Tax benefits associated with green building practices
Looking at the cost per kilogram of a PEB structure shows big financial gains. Banks are now supporting green warehouse projects. They see the long-term value.
PEB projects can pay off faster. They have:
- Shorter construction times
- Lower operating costs
- Less maintenance needed
- Better structural efficiency
Our study shows PEB investments can pay off 30-40% faster than traditional buildings. Using Building Information Modeling (BIM) can save 10-20% in planning and execution.
Businesses gain a lot from PEB investments. Modular construction can cut costs by up to 25%. PEB structures are also easy to expand. They are a smart choice for companies looking ahead.
Quality Assurance and Warranty Considerations
Pre-engineered building (PEB) solutions are at the top of structural engineering. Quality assurance is key to ensure they last long and perform well. The cost of building a PEB is affected by strict quality control.
We are dedicated to excellence. Our testing standards are high to ensure safety and durability. The cost of a PEB warehouse shows our big investment in quality control.
Advanced Testing Standards
- Non-destructive testing techniques for component integrity
- Comprehensive material strength verification
- Compliance with international building codes
- Structural load resistance assessments
Certification Requirements
We follow strict certification processes. This makes sure our PEB structures are top-notch. Key criteria include:
- International Building Code (IBC) compliance
- American Institute of Steel Construction (AISC) standards
- National Fire Protection Association (NFPA) safety specifications
Our quality control practices ensure PEB solutions are exceptionally resilient. They last long and perform well. This reduces risks and boosts client confidence.
Future Market Trends and Cost Projections
The Pre-Engineered Building (PEB) market in India is set for big growth. It’s expected to grow at 11.66% each year from 2023 to 2030. By 2030, it could be worth $50.72 billion.
Changes in the market are affecting the cost of PEB industrial sheds and the cost per square foot. New technologies are making these buildings more appealing to businesses in many fields.
- Technological Integration: Advanced Building Information Modeling (BIM) is improving PEB design accuracy
- Sustainability Focus: Green building methods are becoming key in PEB development
- Market Expansion: Demand is rising in Tier 2 and Tier 3 cities
The commercial and industrial sectors are changing a lot. Warehouses, logistics centers, and factories are choosing PEBs more often. They like them because:
- They are cheaper (20-30% less than traditional buildings)
- They can be built fast
- They last a long time (25-50 years)
Government plans like “Make in India” and smart city projects are helping PEBs grow. With new tech and a focus on green buildings, the future of PEBs looks bright.
Conclusion
Pre-engineered buildings (PEBs) are changing the game for businesses. They offer affordable, portable cabins and strong container office designs. With a 90% recyclability rate and saving 27%-30% in materials, they’re making a big impact in India.
PEBs are a smart choice for businesses. They save time and money, and are good for the environment. They can be used for many things, like manufacturing sheds and farms. This makes them very flexible for different needs.
In India, PEBs are leading the way in building technology. They make it possible for businesses to have affordable, portable offices. With their durability and cost savings, PEBs are a smart choice for companies.
We encourage businesses to think about using PEB technology. It can help them be more efficient, sustainable, and grow. The future of building is here, and it’s all about precision, adaptability, and meeting the needs of today’s businesses.