PEB Building Construction Cost: Key Insights for Cost-Effective Steel Structures
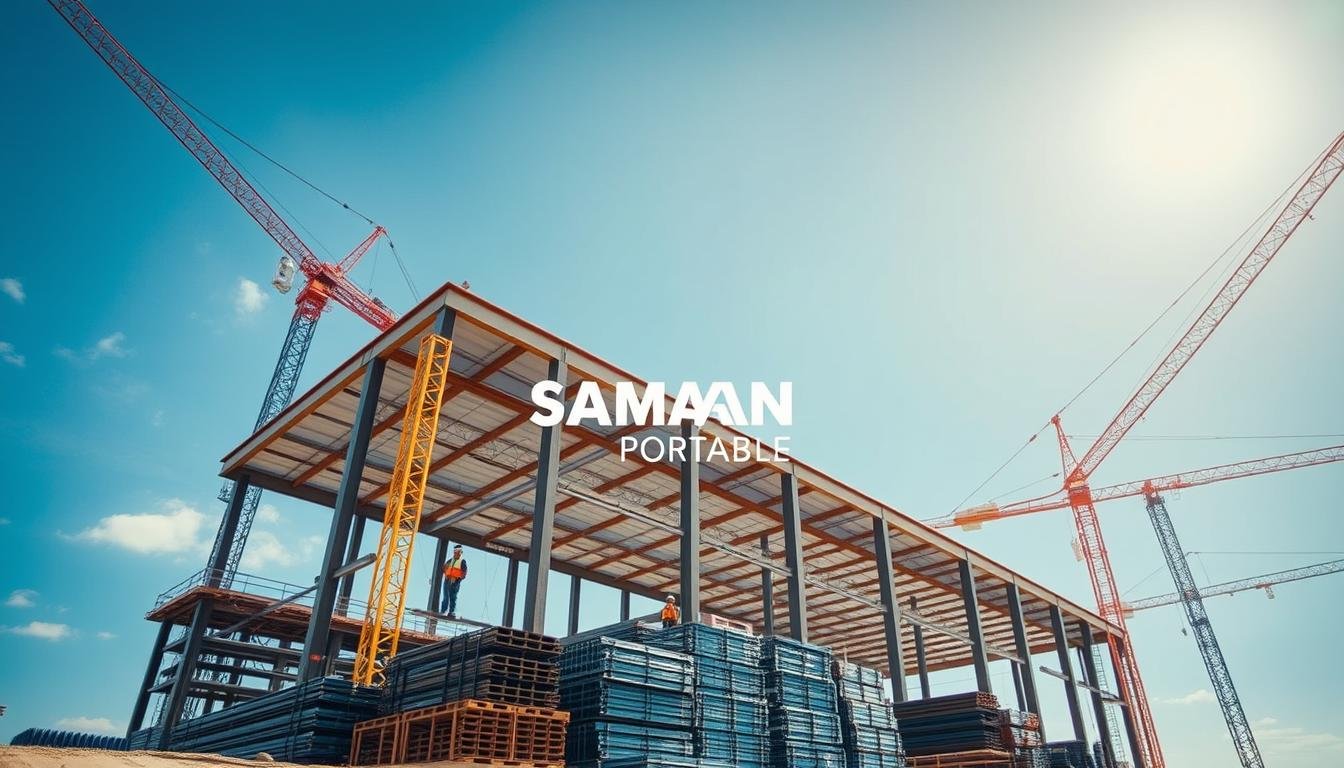
Are you ready to change how you build with a method that cuts costs and speeds up projects? Pre-Engineered Building (PEB) systems are a big leap forward in construction. They bring unmatched efficiency and savings.
In India’s fast-paced construction world, the cost of PEB buildings is key for companies looking for new ways to build. The global PEB market, worth USD 18.51 billion in 2023, shows the huge promise of this new building method.
More builders and developers are choosing PEB technology to improve their building plans. With costs in India from Rs. 300 to Rs. 600 per square foot, PEB buildings are a strong choice over old building ways.
Key Takeaways
- PEB systems can reduce construction costs by up to 30%
- Global PEB market shows robust growth with 11.10% CAGR
- Construction time can be reduced by 50% compared to traditional methods
- Material efficiency leads to significant cost savings
- Flexible design options for various industrial and commercial applications
- Sustainable and environmentally friendly construction approach
- Reduced labor and installation expenses
Understanding Pre-Engineered Building Systems
Pre-engineered building (PEB) systems are a game-changer in construction. They bring efficiency and cost savings to industrial and commercial projects. This approach has changed how businesses build.
Core Components and Features
The key parts of PEB structures are:
- Primary steel framework
- Secondary framing elements
- Roof and wall sheeting systems
- Precision-engineered connection details
PEB systems are made in a standard way, which saves money. They can be up to 30% lighter than traditional steel buildings. This means less material and lower transport costs.
Modern Applications in Construction
PEB structures are used in many fields, including:
- Warehouses and logistics centers
- Manufacturing facilities
- Agricultural buildings
- Commercial complexes
In India, PEB costs range from Rs. 300 to Rs. 600 per square foot. This makes them a cost-effective choice for building quickly.
Benefits of PEB Technology
PEB structures offer many benefits, such as:
- Reduced construction time – up to 50% faster than traditional methods
- Minimal on-site fabrication requirements
- High structural precision
- Flexibility for future expansions
PEB systems are very adaptable, driving innovation in construction. They are becoming a top choice for businesses looking to the future.
Current Market Trends in PEB Construction
The pre-engineered building (PEB) market is changing fast. Global trends are shaping how we build. The market is growing, valued at USD 16.5 billion in 2024. It’s expected to hit USD 40.94 billion by 2033.
What’s driving PEB construction? Here are the main trends:
- Rapid urban population growth of 2.3% in 2023
- Increasing demand for PEB warehouses across industrial sectors
- Rising adoption of cost-effective building solutions
- Significant growth in infrastructure development
The cost of building with PEB has dropped. This makes PEB warehouses a great choice for businesses. In India, the construction industry is growing fast, at 15.7% CAGR from 2021 to 2026. This is boosting PEB use.
What’s shaping PEB construction? Here are the key factors:
- Asia-Pacific region leads with 2.7% urban population growth
- Industrial sector shows 18% increase in PEB steel structure demand
- E-commerce expansion driving warehouse construction
- Smart building technologies integration
The future of construction is in adaptable, cost-effective, and sustainable solutions. PEB technologies provide these.
PEB Building Construction Cost: Essential Factors
It’s key to know what affects peb building construction cost for good project planning. Companies looking for efficient solutions must understand pricing and value well.
The cost of a peb structure per square foot depends on many things. These factors can greatly change the project’s total cost. Investors and managers need a detailed plan for budgeting and managing costs.
Material Cost Variables
Material costs are a big part of PEB project budgets. Important things to think about include:
- Structural steel frames make up 60-70% of the total costs
- Choosing the right steel grade (E250 and E350 are common)
- Improving material efficiency can save 15-30% of costs
Labor and Installation Expenses
Labor is a big factor in peb building construction cost. Smart strategies can lead to big savings:
- Labor costs can drop by 20% with PEB technology
- Installation costs are usually 10-15% of the budget
- Building times can be cut by up to 50% compared to old methods
Regional Price Differences
Prices vary by location. In India, peb structure cost per square foot is between Rs. 300 to Rs. 600. Worldwide, prices range from $10 to $25 per square foot.
Knowing these detailed cost factors helps leaders make better budgets. It also helps find ways to save money on PEB projects.
Cost Comparison with Traditional Construction Methods
Pre-engineered building (PEB) construction saves a lot of money compared to old ways of building. It uses new designs and building methods to cut costs. This helps businesses save a lot of money.
PEB construction has many cost benefits:
- It can cut total project costs by up to 30%.
- Labor costs are 20% lower.
- Building time is 30-50% shorter.
- It uses less material, reducing waste.
Portable cabins are another big plus of PEB technology. They offer flexible solutions for many industries. This includes construction sites and temporary offices.
Looking at key metrics shows PEB’s economic benefits:
- Material Efficiency: PEB needs exact material amounts, cutting down on waste.
- Labor Optimization: Its streamlined process means less labor needed.
- Time Management: It builds faster, finishing projects quicker.
Choosing PEB construction means better financial planning. Its standard manufacturing process lowers unexpected costs. It also builds strong, lasting structures that fit many needs.
Material Selection and Quality Standards
Choosing the right materials is key for top-notch PEB structures and modern container offices. The quality of these materials affects how long the building lasts, its cost, and how well it performs.
Steel Grade Considerations
When it comes to PEB structures, picking the right steel is very important. In India, makers often use E250 and E350 steel grades. These offer great strength and dependability. The main things to look at in steel are:
- How much weight it can hold
- How well it resists rust
- How easy it is to weld
- Its price
Component Quality Requirements
High standards are set for PEB structures to meet industry needs. Makers pay close attention to:
- How accurate the dimensions are
- How consistent the materials are
- How well the parts fit together
- Using advanced tests to check for defects
Durability Considerations
Modern container offices need materials that can handle different weather conditions. Using high-quality steel and protective coatings helps them last longer. This means less upkeep and better performance over time.
By focusing on material quality and strict standards, companies can build strong PEB structures. These structures offer great value and reliability.
Design and Engineering Considerations
Design and engineering are key to the cost and success of a PEB project. New technologies have changed how engineers work on pre-engineered buildings. They now make more accurate plans and use materials better.
When making durable porta cabins for industries, there are important things to consider:
- Structural integrity analysis
- Load-bearing capacity assessment
- Material selection optimization
- Cost-effective design strategies
Today’s design uses advanced software like STAAD Pro and Tekla. These tools help engineers make efficient structural models. They cut down on design mistakes and make building faster.
The design phase is about 5-10% of the total project cost. Good engineering choices can lower the final cost of a PEB building. It’s important to plan well and use the latest technology.
Important factors for good PEB design include:
- Precise structural calculations
- Material efficiency
- Sustainability considerations
- Compliance with building codes
By using new design ideas and engineering tech, companies can make strong industrial solutions. These solutions are good for performance, last long, and are affordable.
Foundation Requirements and Site Preparation
Starting a pre-engineered building (PEB) project needs careful site prep and foundation planning. These steps are key to the project’s success and cost. They also affect how well the project runs.
Good foundation design is vital for strong and affordable buildings. It’s even more important for labor colonies. The foundation’s quality affects the building’s strength and how well it lasts.
Soil Testing Requirements
Soil testing is the first step in building a PEB. Experts do detailed tests to learn about the soil. They check things like soil type, how much it can hold, and any environmental issues.
Foundation Types and Costs
There are many foundation types for PEBs, each with its own price tag. Here are a few:
- Shallow foundations: Good for stable ground
- Deep foundations: Needed for tough terrain
- Pile foundations: Best for complex soil
Foundation costs usually make up 10-15% of the total budget. Choosing the right foundation can save money and ensure the building is safe.
Site Development Expenses
Site prep involves several steps:
- Terrain leveling and ground prep
- Drainage system setup
- Connecting to infrastructure
- Building access roads
Managing site development well helps create cost-effective and sustainable labor colonies.
Installation Process and Timeline Impact
Pre-Engineered Buildings (PEB) change how we build, making it faster for businesses. They are perfect for PEB warehouses and trendy container cafes. This is because they cut down on the time needed to set up.
The way PEBs are installed is a big plus. Businesses save a lot of time, with construction times cut by 30% to 50%. Typical delivery times range from 6 to 8 weeks, which is much faster than traditional building.
- Prefabrication allows for rapid on-site assembly
- Minimized labor requirements speed up construction
- Standardized components ensure precise fitting
- Reduced on-site fabrication time
PEB installation has many benefits:
- Projects are finished faster
- Construction costs are lower
- Businesses can grow faster
- There’s less disruption to the site
PEB warehouses and trendy container cafes can be built quickly. This means businesses can start working sooner. They can also avoid long periods of downtime.
Lightweight steel and precise engineering make PEBs fast to install. The modular design also helps. It makes assembly quick, saving on labor and reducing the complexity of traditional building.
Environmental Benefits and Sustainability Features
Modern container office designs and PEB structures are changing the game in sustainable building. They offer big advantages over old construction methods. These benefits are good for businesses and the planet.
Energy Efficiency Aspects
PEB structures are top-notch when it comes to saving energy. They have special features that help:
- Insulated metal panels that keep heat out
- Reflective roofs that don’t absorb too much sun
- Systems to manage temperature
- Smart designs for natural light
Environmental Impact Analysis
PEB structures are really good for the environment. Steel, the main material, has big benefits:
- It’s easy to recycle and keeps its strength
- It has a lot of recycled content
- It makes less greenhouse gases during making
Long-term Sustainability Benefits
Companies that choose modern container offices and PEB structures will see big environmental wins. They’ll use less energy, make less waste, and cut down on carbon emissions. The way these buildings are made also helps the environment by reducing waste and disruption.
The global market for pre-engineered buildings is expected to hit $37,807.3 million by 2026. This shows that these green building solutions are the future of building responsibly.
Maintenance and Long-Term Cost Benefits
Pre-engineered building (PEB) solutions are great for industries looking for durable porta cabins. They offer long-term cost savings and efficient infrastructure. These structures are designed to need little maintenance and work efficiently.
PEB structures have many maintenance benefits:
- They are very durable with high-quality steel parts.
- They resist environmental challenges like rust and corrosion.
- They have lower repair and replacement costs over time.
- They cost less to maintain than traditional buildings.
The cost of PEB buildings is more appealing when you think about their long life. Businesses save a lot of money because:
- Materials don’t degrade as much.
- Maintenance is simpler.
- Structures stay strong.
- Operations are less disrupted.
Steel’s natural properties help PEB structures handle tough industrial settings well. They keep their performance strong. The modular design makes it easy to upgrade and change things. This reduces long-term costs.
Advances in manufacturing have made PEB technologies more affordable. They offer great value in many industrial settings. By focusing on durability and efficiency, businesses can make their infrastructure investments last a long time.
Innovative Applications in Modern Construction
Pre-engineered building (PEB) technology is changing the construction world. It brings new solutions to many sectors. These structures are making infrastructure development more flexible and efficient.
The construction industry is seeing big changes. PEB technology is a key player in creating adaptable spaces. It meets the complex needs of businesses.
Commercial Spaces Reimagined
Trendy container cafes are becoming a hit in business architecture. They use PEB technology for unique dining experiences. These include:
- Rapid deployment capabilities
- Cost-effective design solutions
- Modular and scalable configurations
- Customizable aesthetic options
Industrial Solutions
Industrial sectors are turning to PEB technology for better manufacturing and storage. It helps create efficient labor colonies with:
- Streamlined construction processes
- Reduced overall project timelines
- Enhanced worker comfort
- Sustainable infrastructure design
Specialized Structural Innovations
PEB technology goes beyond usual uses. It makes specialized structures like research facilities and logistics centers. These solutions let businesses quickly adjust to new needs.
With a 7.40% annual growth in India, PEB technologies are set to change construction in many industries.
Future Trends and Cost Projections
The pre-engineered building (PEB) market in India is set for big growth. It’s expected to grow at a rate of 11.66% from 2023 to 2030. The market value could hit $50.72 billion. This growth shows more people want affordable and modern building solutions.
Several trends are shaping the future of PEB structures:
- Advanced technologies reducing peb structure cost per sq ft
- Innovative modern container office designs
- Enhanced sustainability practices
- Integration of digital technologies like Building Information Modeling (BIM)
Costs are changing fast. The cost of pre-engineered metal buildings is between $10 and $25 per square foot. In India, prices range from Rs. 300 to Rs. 600 per square foot. Most of the cost goes to the structural steel frames, making up 60-70% of the total.
New technologies are making PEB construction better. Modular design approaches cut down on waste and labor costs. They also make projects finish faster. Government plans like “Make in India” and smart city projects are pushing for these advanced systems.
Sustainability is a big deal now. PEBs are more energy-efficient, helping with green building goals. They can save up to 70% on maintenance and cut construction time by 30-50%. These buildings are the future of efficient building.
Conclusion
PEB Building Construction Cost is changing how we build in India. It offers businesses flexibility and saves money. Portable cabins show how these buildings can fit many needs.
Steel-based PEBs cut down on costs and time. They save money and speed up building. This means projects can start sooner and stay on budget.
PEB solutions are a smart choice for building. They mix new design with green manufacturing. This makes them a great option for quick and cost-effective projects.
In India’s growing infrastructure, PEBs lead the way. They mix savings, speed, and green design. This makes them key for businesses looking to the future.
FAQ
What are Pre-Engineered Buildings (PEB) and how do they differ from traditional construction?
Pre-Engineered Buildings (PEB) use steel parts made off-site and put together on-site. They are faster, more customizable, and cheaper than traditional buildings. PEBs are great for many uses, like industrial and commercial spaces.
How does the cost of PEB construction compare to traditional building methods?
PEB buildings can save 30-40% compared to traditional ones. This is because they use less material, build faster, and cost less in labor. Their design is also more efficient, making them a smart choice for building.
What factors influence the overall PEB building construction cost?
Several things affect PEB costs. These include the type of steel, how complex the design is, and the site conditions. Prices also vary by region and what the project needs. Material and labor costs, along with how efficient the build is, all matter.
Are PEB structures suitable for different types of applications?
Yes! PEBs work for many uses. They’re good for warehouses, offices, and even special buildings. Their flexibility makes them a great choice for many needs.
What are the environmental benefits of choosing PEB structures?
PEB buildings are good for the planet. They waste less material, use less energy, and are made to last. They help reduce carbon footprint and support green building.
How long does a typical PEB structure last?
With care, PEBs can last 25-50 years. Their design and materials help them last longer. This makes them a smart choice for businesses looking to save money in the long run.
Can PEB structures be customized to specific business needs?
Yes, PEBs can be made to fit your business. You can change the design, use different materials, and add special features. This means PEBs can be tailored to meet your exact needs.
What maintenance considerations are important for PEB structures?
PEB buildings need little upkeep. Just regular checks, cleaning, and rust prevention. Their design and materials mean they cost less to keep up over time.
How quickly can a PEB structure be constructed?
PEB buildings are built 40-60% faster than usual. They can take 4-12 weeks, depending on size and complexity. Their off-site making and quick assembly make them fast.
What economic advantages do PEB structures offer for businesses?
PEB buildings save businesses money. They cost less upfront, run cheaper, and pay back faster. They’re also easy to grow with and make operations more efficient. This makes them a smart choice for businesses looking to save.