Understanding PEB Structure Cost per Sq Ft: Affordable Steel Building Solutions
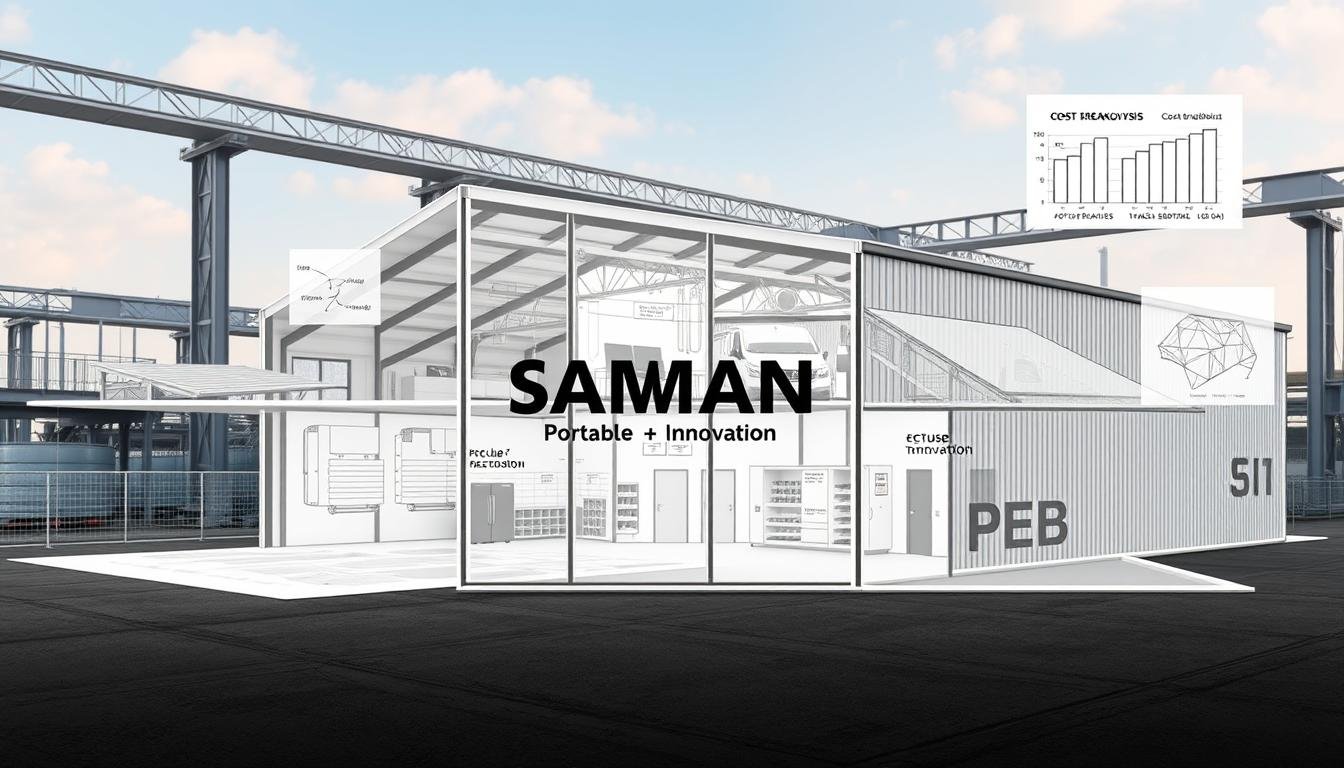
Are you looking for a way to save time and money in construction? Pre-Engineered Buildings (PEB) could be the answer you need.
The cost of PEB structures per square foot is a game-changer in building. Prices worldwide range from $10 to $25 per square foot. In India, prices are even better, from Rs. 300 to Rs. 600 per square foot.
Steel-based PEB technology is very flexible in construction. It uses advanced engineering to cut construction time by up to 30%. It also improves material use by 40%.
PEB solutions are great for businesses wanting to save money and build fast. They work well for many industrial and commercial needs.
Key Takeaways
- PEB structures offer cost-effective building solutions
- Construction time can be reduced by up to 30%
- Material efficiency improvements reach 40%
- Competitive pricing across global markets
- Versatile applications in multiple industry sectors
Introduction to Pre-Engineered Building Systems
Pre-Engineered Building (PEB) systems are changing how we build today. They offer a new way to design and construct buildings. This method is flexible and saves money.
PEB structures have grown a lot in recent years. They use the latest designs and manufacturing methods. This makes building fast, precise, and tailored to many needs.
Evolution of PEB Technology
The PEB technology has seen big steps forward:
- First, there were standard steel frames.
- Then, computer-aided design (CAD) was added.
- Next, new materials and science came into play.
- Lastly, better computer models were used.
Core Components Overview
PEB structures have key parts that help keep costs down:
- Primary steel framing
- Secondary structural members
- Roof and wall sheeting systems
- Structural connections
- Foundation systems
Modern Applications in Construction
PEB technology is used in many fields. This includes manufacturing, warehouses, farms, and offices. It lets builders create unique solutions that fit their needs and stay affordable.
In India, PEB structures cost between Rs. 300 to Rs. 600 per square foot. They are cheaper than traditional building methods. They also save time and reduce waste, making them popular with smart builders.
Current Market Trends and Growth Projections
The pre-engineered buildings (PEB) market in India is changing fast. Recent data shows the market for PEB warehouses and labor solutions is growing. It was worth USD 0.4686 billion in 2023 and is expected to hit USD 0.888 billion by 2032.
Important market insights show big changes in the industry:
- Compound annual growth rate (CAGR) of 7.40% from 2024 to 2032
- Steel segment accounting for 35% of market revenue
- Commercial property leasing growing by 30% in Q1 2019
Several key factors are driving the demand for PEB warehouses:
- Increased manufacturing plant expansions
- Rising need for distribution centers
- Growing infrastructure investments
New trends suggest a big chance for efficient labor solutions in many areas. The single-story segment is leading the market, with commercial use growing fast. Indian makers like EPACK Prefab are boosting production to meet the growing demand.
The pre-engineered buildings market is a fast-changing world of innovation and strategic building. As companies look for flexible and affordable building options, PEB technologies are changing how buildings are made in India.
PEB Structure Cost per Sq Ft: A Detailed Look
Understanding the cost of Pre-Engineered Buildings (PEBs) is complex. It involves looking at many factors. The cost per square foot is key for businesses and developers looking for cost-effective construction.
Base Cost Breakdown
The main costs of PEB structures include:
- Raw material expenses (steel and secondary components)
- Fabrication and manufacturing costs
- Design and engineering fees
- Transportation and logistics
- On-site installation expenses
Regional Price Variations
PEB building costs vary by region. In India, prices are between Rs. 300 to Rs. 600 per square foot. This is due to local market conditions, material availability, and labor costs.
Cost-Influencing Factors
Several factors affect the cost of PEB structures per square foot:
- Building complexity – Complex designs raise manufacturing and installation costs
- Project size and total square footage
- Specific structural needs
- Customization level
- Regional labor and material prices
Specialized PEB makers use standard parts and efficient designs to cut costs. They can save 6-8 weeks in fabrication time and up to 30% in weight. This leads to more affordable construction.
Primary Components of Steel Building Structures
Pre-engineered building (PEB) structures are a modern and cost-effective way to build. They use innovative designs and focus on saving money. The framework of PEB structures has key parts that affect how well they work and their cost.
The main parts of steel building structures are:
- Primary Steel Frames: These are the main support and strength of PEB structures
- Secondary Framing Systems: These add extra support to the main frames
- Roofing and Wall Panels: They protect the building from the weather and help keep it cool
- Connection Details: These are important for keeping the structure stable
Steel makes up 60-70% of the cost in PEB construction. This shows how important choosing the right materials is. The global PEB market was worth USD 18.51 billion in 2023. This shows more people are choosing these advanced buildings.
PEB structures have many benefits, including:
- They can save up to 30% compared to traditional building
- They are built faster, usually in 6-8 weeks
- They are lighter, which means less weight on the structure
Choosing the right parts is key to the cost and performance of PEB structures. Engineers carefully pick materials and designs to make the best buildings.
Material Selection and Quality Standards
Choosing the right materials is key to saving on PEB building costs. Pre-engineered buildings (PEB) use top-quality steel. This steel affects how well and long the buildings last.
Building great PEB structures starts with picking the right materials. Companies pick steel grades that meet strict quality and performance standards.
Steel Grade Options
PEB buildings use different steel grades for strength:
- E250 grade steel for everyday use
- E350 high-tensile steel for more strength
- Special alloys for tough industrial settings
Quality Certification Requirements
Quality checks keep PEB building costs down and quality up. Important standards include:
- International material tests
- Checking if structures are strong
- How they do in harsh weather
Material Performance Metrics
Today’s PEB buildings are tested with advanced metrics. These check:
- Tensile strength and how much weight they can hold
- How well they resist rust
- How long they last
- How they handle heat and stress
By focusing on material quality, engineers make PEB structures that last longer, cost less to maintain, and offer great value.
Construction Timeline and Efficiency Benefits
Pre-engineered building (PEB) structures change the game in construction timelines. They offer big cost savings, making them a top pick for many projects. Businesses see their project times cut in half, thanks to advanced engineering.
PEB construction brings many benefits:
- Construction time is cut by 30-50%
- Project management gets smoother
- Less labor is needed on-site
- Project schedules are more predictable
Building efficient labor colonies is easier with PEBs. The standard manufacturing process means parts are made with high precision. This leads to quick assembly on-site. Teams can finish complex projects in weeks, not months.
Technical advancements drive these gains:
- Factory-made parts are made with precision
- Parts are designed to fit together easily
- Advanced CAD tech is used
- Engineering specs are exact
The cost savings are huge. PEB structures can cut project costs by up to 45%. This makes them a favorite for many projects in industries like construction and infrastructure.
Design and Engineering Considerations
Design and engineering are key to making PEB structures efficient and meeting various architectural needs. Professional engineering services usually cost 5-10% of the total project budget. This shows how important a good design strategy is.
Modern container office designs need advanced engineering to work well and save money. Architects and engineers use top-notch computer tools to create detailed structural plans.
Structural Analysis Methods
Structural analysis uses several important methods:
- 3D computational modeling
- Finite element analysis
- Dynamic load simulation
- Stress and strain evaluation
Custom Design Options
PEB structures are very flexible for customizing. Designers can change building layouts to fit specific needs, such as:
- Modular office layouts
- Flexible interior spaces
- Scalable architectural designs
- Adaptive building systems
Technical Specifications
Technical specs are vital for a structure’s strength. Important factors include material choice, load-bearing capacity, and how it handles the environment. Precise engineering calculations ensure the building performs well and stays affordable.
Foundation Requirements and Site Preparation
Foundation design is key in the cost of building PEB warehouses. It usually takes up 10-15% of the total budget. Choosing the right foundation is important for the building’s strength and cost.
Preparing the site for PEB warehouses involves several steps:
- Comprehensive soil analysis
- Terrain evaluation
- Load-bearing capacity assessment
- Drainage and ground stability
There are different foundation types for various needs:
- Slab-on-grade foundations: Best for stable ground
- Deep foundations: Needed for tough soil
- Pile foundations: Good for weak ground
The location of PEB warehouses affects foundation design. Remote sites can be more expensive due to transport and prep costs. Engineers check the local geology to find the best foundation, keeping costs low and stability high.
Good site prep avoids future structural problems. It’s a smart investment in the project’s life. Knowing these foundation needs helps developers plan better and stay within budget.
Labor and Installation Cost Analysis
Pre-engineered building (PEB) construction is a game-changer in labor management and installation. It has greatly improved infrastructure development in India. This is thanks to a smart approach to managing costs.
Looking into labor needs shows big advantages in PEB construction. Solutions for efficient labor colonies are key. They help make projects run smoothly and cut down costs.
Skilled Labor Requirements
PEB structures need a special team with certain skills. The installation process requires:
- Structural steel fabrication experts
- Precision welding professionals
- Advanced rigging and installation technicians
- Quality control specialists
Installation Time Estimates
PEB construction saves a lot of time. Here are some key points:
- Construction time can be cut by up to 50%
- Workforce productivity goes up by 30-40%
- Installation costs are usually 10-15% of the total budget
The PEB method makes projects finish faster. It uses precision-engineered components. This leads to big cost savings and quicker completion times.
Environmental Impact and Sustainability Features
PEB structures are a big step forward in building, with huge environmental benefits. They use less material and energy than old ways of building.
PEB structures have many good points for the environment:
- They are up to 30-35% lighter than regular steel buildings.
- They need less material to make.
- Steel parts can be recycled easily.
- They make less carbon pollution during building.
Modern container offices use PEB tech for green workspaces. They use smart design to cut down on harm to the planet. Plus, steel is recyclable, so PEB buildings can be reused or recycled later.
PEB structures also have other green features:
- They keep heat better.
- They can use green tech.
- They use less energy.
- They need less upkeep over time.
The future of building is about green, flexible solutions that work well and protect the planet. PEB structures lead the way, helping businesses be kinder to the earth without sacrificing quality.
Maintenance and Long-term Cost Benefits
Pre-engineered building (PEB) structures offer great long-term savings. They are better than traditional buildings in many ways. Knowing the upkeep and cost savings of PEB warehouses helps businesses make smart choices.
PEB structures have big financial benefits over their lifetime. With regular care, they can last for many years. This makes them a good choice for companies looking to save money.
Regular Maintenance Schedule
Keeping PEB structures in top shape is key. Here are some important maintenance steps:
- Annual structural inspections
- Periodic coating and rust prevention
- Checking structural connections and fasteners
- Monitoring roof and wall panel integrity
- Maintaining drainage systems
Cost Savings Over Time
PEB buildings save money in many ways. Businesses can enjoy big financial benefits:
- Lower maintenance costs than traditional buildings
- Energy savings, which cuts down on operational costs
- Less need for repairs
- Up to 30% in lifecycle savings
The PEB market is growing fast, at 8.48% CAGR. Investing in PEB warehouses helps companies save money. It also ensures their buildings last long and work well.
Comparing PEB with Traditional Construction Methods
Pre-engineered buildings (PEB) have changed the construction world. They offer a clear choice over old building ways. The cost of PEB structures per square foot shows why modern methods are better, both in money and practicality.
PEB and traditional building differ in many ways:
- Construction Speed: PEB can cut construction time by up to 50%
- Cost Efficiency: Save 30-50% on initial construction costs
- Material Optimization: Use 15-30% less material
- Design Flexibility: Use advanced CAD for precise designs
The cost benefits of PEB buildings are clear when looking at expenses. Steel frames make up 60-70% of costs, making PEB a cost-effective choice. Labor costs can fall by 20%, and foundation work needs less time and resources than old methods.
Construction experts are seeing the value in PEB. The global PEB market is growing fast, expected to hit USD 0.888 billion by 2032. This shows PEB’s growing popularity and success in providing affordable, efficient buildings.
In the end, PEB structures are a new way to build. They offer speed, precision, and savings that traditional methods can’t match.
Industry Applications and Versatility
Pre-engineered building (PEB) systems have changed how we build across many industries. They are flexible for different business needs, from warehouses to trendy container cafes.
PEB structures are adaptable, making them a big deal for many sectors. Companies use them to make efficient and affordable spaces that fit their needs.
Key Application Areas
- Industrial warehouses and logistics centers
- Commercial complexes
- Agricultural facilities
- Institutional buildings
- Trendy container cafes
- Manufacturing plants
One big plus of PEB warehouses is how fast they can be built. They can be up to 50% faster than traditional buildings. This also means saving 15-30% on costs.
Economic Benefits
- Reduced construction costs
- Faster project completion
- Customizable design options
- Long-term maintenance advantages
PEB structures are a game-changer for modern building, giving businesses flexibility and saving money. They are great for building everything from high-tech warehouses to unique container cafes.
Safety Standards and Building Codes
Understanding safety regulations is key for PEB structures and portable cabins. Following national and local building codes is essential. It ensures the structure is safe and strong.
PEB structures must meet strict safety standards. These standards cover important areas:
- Structural integrity assessments
- Wind load resistance
- Seismic performance requirements
- Fire safety specifications
- Environmental durability
Regulatory Compliance Essentials
PEB structures must follow quality standards like IS2062 and ASTM572. Manufacturers need to show:
- Precise material grade specifications
- Comprehensive structural testing
- Performance documentation
- Quality control certification
Safety Certifications
Getting safety certifications for PEB structures is a detailed process. Key certification processes include:
- Detailed structural analysis
- Load-bearing capacity tests
- Material performance verification
- Independent third-party inspections
By focusing on safety, PEB structures offer reliable and secure solutions. They give peace of mind to everyone involved in the project.
Future Trends in PEB Construction
The world of PEB structures is changing fast. New technologies and market needs are driving these changes. Pre-engineered buildings are becoming key in making buildings more sustainable and efficient.
Some big trends in PEB construction are:
- Advanced technological integration with Building Information Modeling (BIM)
- Expansion into Tier 2 and Tier 3 cities across India
- Growing adoption of modern container office designs
- Increased focus on sustainable and energy-efficient solutions
The Indian PEB market is growing fast. It’s expected to grow by 11.66% each year from 2023 to 2030. The market value could hit $50.72 billion. This shows how PEB structures are changing the construction world.
New technologies are changing PEB construction. Modern container offices are now more advanced. They offer flexible spaces for businesses. These designs use strong steel and insulation to save costs and be efficient.
- PEB systems can reduce construction time by up to 50%
- Material efficiency leads to 15-30% cost savings
- Structures can be relocated, providing unprecedented flexibility
Government support for green building is helping PEB technology grow. The future of building is looking modular, green, and tech-savvy.
Conclusion
Pre-engineered building (PEB) structures are a big step forward in construction. They offer cost savings and efficiency, making them a great choice for many industries. The cost per square foot, from INR 1,500 to INR 2,500, is lower than traditional methods.
PEB structures are not just cheaper. They also save time and materials. This means they can be built up to 30% faster and use 40% less material. The global market is growing fast, expected to hit $32.8 billion by 2033.
In India, PEB structures are a smart choice for businesses. They can be made to fit specific needs and are built 50% quicker than old methods. They also save 20-40% on energy costs and last over 30 years.
PEB structures lead the way in building technology. They are sustainable and efficient. Knowing the cost per square foot helps businesses save money and work faster in today’s fast-paced world.
FAQ
What are Pre-Engineered Buildings (PEB) and how do they differ from traditional construction?
Pre-Engineered Buildings (PEB) are made in a factory and put together on-site. They are different from traditional buildings because they are more precise, faster to build, and cheaper. They use advanced engineering and steel parts to make buildings that can be used in many ways.
How much does a PEB structure typically cost per square foot?
PEB structures cost between and per square foot. This price changes based on how complex the building is, where it’s located, and what custom features it needs. The final cost also depends on the local market, the quality of materials, and the design.
What are the primary advantages of choosing a PEB structure?
PEB structures are built quickly and are cost-effective. They are flexible in design, need less labor, and have less waste on-site. They are strong and can be easily expanded in the future. This makes them a faster and cheaper option than traditional buildings.
How long does it take to construct a PEB building?
Building a PEB structure is 30-50% faster than traditional methods. A medium-sized warehouse or industrial building can be ready in 3-6 months. This is much faster than the 6-12 months it takes for traditional buildings.
Are PEB structures suitable for different industrial applications?
Yes, PEB structures are very versatile. They can be used for warehouses, manufacturing, commercial spaces, agricultural buildings, and even portable offices. Their design can be customized for almost any industrial or commercial need.
What maintenance is required for a PEB structure?
PEB structures need very little maintenance. It’s recommended to do annual inspections, clean them regularly, and check the paint and coating. You should also address any corrosion or structural issues. The steel used in PEB structures is durable and requires low maintenance costs.
Can PEB structures be environmentally sustainable?
Yes, PEB structures are sustainable. They reduce waste, are energy-efficient, and use recyclable steel. They can also include green building features and have a lower carbon footprint than traditional buildings.
How do regional variations impact PEB structure costs?
PEB structure costs change based on local material prices, labor rates, and transportation costs. Building codes and market demand in the region also play a role. Factors like steel prices and economic conditions affect the overall cost of the project.
What types of steel are typically used in PEB structures?
PEB structures mainly use high-strength, corrosion-resistant steel. Grades like ASTM A36, ASTM A572, and weathering steel are commonly used. The choice depends on the project’s needs, the environment, and the structural requirements.
How customizable are PEB structures?
PEB structures can be customized in many ways. You can choose different heights, widths, roof styles, wall treatments, colors, and interior layouts. They can also include features like mezzanine floors, crane systems, and special architectural elements.